Digital Type High Precision Contactless Angle Sensor
Introduction
ER-AS-26 angle sensor is combined with an embedded microprocessor and a numerical control angle secondary calibration device. Program calibration conversion can achieve high accuracy, low temperature drift, and low power consumption. Digital output has RS232, RS485, TTL, MODBUS (optional), reaching high resolution: 0.015°, high precision: 0.05°, output ratio: 100HZ.
The magnetic sensitive angle sensor has the characteristics of non-contact, long life, high resolution, low temperature drift, good linearity, fine reset, high frequency response, multiple protections, anti-interference, anti-vibration, and anti-shock characteristics, that is suitable for water, oil, gas, vibration, shock, especially harsh industrial environments, are also ideal alternatives to contact angle sensors (such as conductive plastic potentiometers).
Features
Sampling rate: 1K HZ
Full range accuracy 0.05°
Output RS232, TTL, RS485, MODBUS optional
Wide voltage input DC 9~36V
Wide temperature working -40~+85℃
Angular resolution is 0.015°
High vibration resistance >20000g
IP66 protection level
Range 0~360°(optional)
Linearity is 0.15%~0.5%
Applications
Railway gauge
Satellite solar antenna positioning
Towed motor control
Mining machinery, oil logging equipment
Medical equipment
Liquid valve: angle actuators
Angle-based control
Various construction machinery angle control
Textile machinery
Specifications
Parameter | Condition | ER-AS-26-90 | ER-AS-26-180 | ER-AS-26-270 | ER-AS-26-360 | Unit |
Measuring range | / | 0~90 | 0~180 | 0~270 | 0~360 | ° |
Temperature drift | -40~85° | ±0.0015 | ±0.0015 | ±0.0015 | ±0.0015 | °/℃ |
Temperature coefficient of sensitivity | -40~85° | <150 | <150 | <150 | <150 | ppm/℃ |
Frequency response | DC response | 100 | 100 | 100 | 100 | Hz |
Resolution | / | 0.012 | 0.012 | 0.012 | 0.012 | ° |
Precision | -40~85℃ | 0.05 | 0.06 | 0.08 | 0.1 | ° |
Long-term stability | -40~85℃ | 0.055 | 0.063 | 0.08 | 0.12 | ° |
Output interface | / | RS232, TTL, RS485, MODBUS Optional | ||||
Power on start time | / | 0.2 | 0.2 | 0.2 | 0.2 | s |
The response time | / | 0.01 | 0.01 | 0.01 | 0.01 | s |
Average working time | ≥55,000 hours/time | |||||
Impact resistant | 20000g, 0.5 ms, 3 times/shaft | |||||
Shock resistant | 10grms, 2~2000Hz | |||||
The use of temperature | -40~85℃ | |||||
Waterproof level | IP66 | |||||
Cable | Standard 1.5m length, wear resistance, oil proof, wide temperature, shielding cable 4*0.3mm² | |||||
Weight | 180g (excluding boxes) |
Electrical information
Parameters | Condition | Min | Typical Value | Max | Unit |
The power supply voltage | / | 9 | 12 | 36 | V |
Reverse power protection | / | / | 20 | / | V |
Signal reverse protection | / | / | 20 | / | V |
The output load | Resistivity | / | 2 | / | KΩ |
Working temperature | / | -40 | / | 85 | ℃ |
Storage temperature | / | -55 | / | 100 | ℃ |
Application Techniques
1.Dip angle sensor method for measuring bridge deflection
2.Determination of Initial Attitude Angle of MEMS Inertial Sensor
3.What Performance is the Accelerometer Sensor in FOG North Finder
4.Calibration Method of Angular Velocity Sensor for Single-axis Speed Turntable
5.Principle and Characteristics of Angular Velocity Sensor
6.Analysis of Typical Applications of MEMS Sensors
More Products
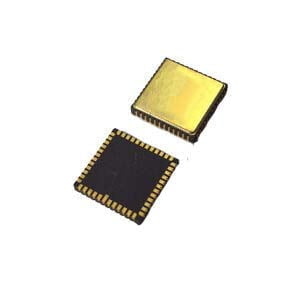
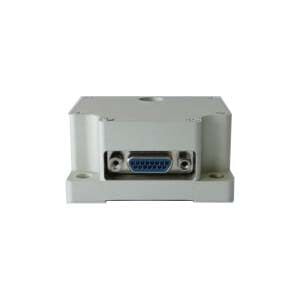
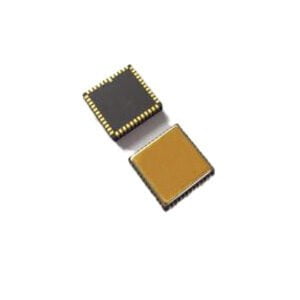
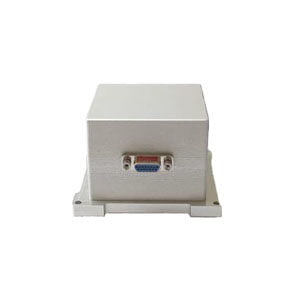
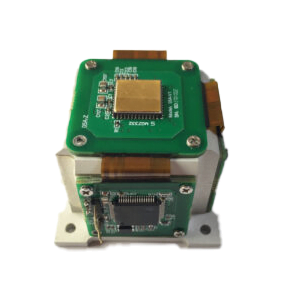
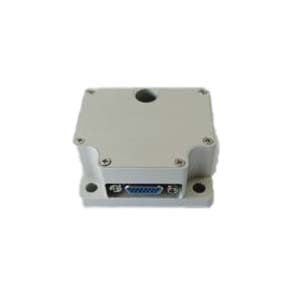