Introduction to IMU
An inertial measurement unit is a device that measures the three-axis angular velocity and acceleration of an object. In a narrow sense, an IMU is equipped with gyroscopes and accelerometers on three orthogonal axes, with a total of 6 degrees of freedom, to measure the angular velocity and acceleration of objects in three-dimensional space. This is what we know as a "6-axis IMU"; in a broad sense, The IMU can add a magnetometer to the accelerometer and gyroscope, forming a "9-axis IMU".
Accelerometer: detects acceleration signals of three independent axes of the carrier coordinate system;
Gyroscope: detects the angular velocity signal of the carrier relative to the navigation coordinate system;
Magnetometer: Use algorithms such as Kalman or complementary filtering to provide users with absolute reference pitch angles, roll angles and heading angles.
The 9-axis sensor with added magnetometer is also called AHRS (Attitude and Heading Reference System). Because the heading angle has a reference to the geomagnetic field, it will not drift. However, the geomagnetic field is very weak and is often interfered by surrounding objects with magnetic fields. The more orthogonal the magnetic field and gravity field are, the better the attitude measurement effect will be. That is to say, if the magnetic field and gravity field are parallel, such as the geomagnetic north and south poles, AHRS cannot be used.
How an accelerometer works
An accelerometer is a sensor that measures acceleration. Accelerometers manufactured by traditional mechanical processing methods are large in size, mass, and cost, and their applications are greatly limited. With the development of Micro Electro Mechanical System (Micro Electro Mechanical System) technology, the development of micro accelerometers has been regarded as a priority project for the productization of Micro Electro Mechanical Systems at home and abroad. Compared with ordinary accelerometers, microaccelerometers have many advantages: small size, light weight, low cost, low power consumption, good reliability, etc. It can be widely used in aerospace, automotive industry, industrial automation and robotics and other fields, and has broad application prospects.
The essence of an accelerometer is to detect force rather than acceleration, that is, the detection device of the accelerometer captures the inertial force that causes acceleration, and then Newton's second law can be used to obtain the acceleration value. The measuring principle can be represented by a simple mass, spring and indicator.
The accelerometer adopts the "Northeast Sky" coordinate system (ENU): g = (0, 0, −9.81) T g= (0, 0, -9.81)^T g= (0, 0, −9.81) T.
An accelerometer is a sensor that measures acceleration. It usually consists of mass block, damper, elastic element, sensitive element and adjustment circuit. During the acceleration process, the sensor uses Newton's second law to obtain the acceleration value by measuring the inertial force exerted on the mass block. The structure includes a silicon diaphragm, an upper cover, and a lower cover. The diaphragm is between the upper cover and the lower cover and is bonded together. One-dimensional or two-dimensional nanomaterials, gold electrodes and leads are distributed on the diaphragm, and a pressure welding process is used to lead out the leads. Depending on the sensor sensitive components, common acceleration sensors include capacitive, piezoresistive, piezoelectric, etc.
How gyroscopes work
When a particle moves in a straight line relative to the inertial system, its trajectory is a curve relative to the rotating system due to its own inertia. Based on the rotation system, we believe that there is a force driving the movement trajectory of the particle to form a curve. The Coriolis force is a description of this deflection, expressed as:
That is to say, when the linear motion is placed in a rotating system, the linear trajectory will deviate. In fact, the linear motion problem is not affected by a force. The establishment of such a virtual force is called the Coriolis force.
Therefore, we select two objects in the gyroscope. They are in constant motion, and the phase difference of their movements is -180 degrees. That is, the two mass blocks move in opposite directions but have the same size. The Coriolis forces they generate are opposite, thus forcing the two corresponding capacitor plates to move, resulting in a differential change in capacitance. The change in capacitance is proportional to the angular velocity of rotation. The change in rotation angle can be obtained from the capacitance.
The measurement accuracy of the IMU is mainly determined by the gyroscope used, so the gyroscope is the core component of the navigation system.
How a magnetometer works
A magnetometer is a device that uses the earth's magnetic field to determine the North Pole. The magnetometer can provide data on the magnetic field experienced by the device in each of the XYZ axes. The relevant data is then imported into the microcontroller's processor to provide the heading angle related to the magnetic north pole. This information can be used to detect geographical orientation. The magnetometer uses three mutually perpendicular magnetoresistive sensors. The sensor in each axis detects the strength of the geomagnetic field in that direction.
The picture above shows an alloy material with a crystal structure. They are very sensitive to external magnetic fields, and changes in the strength of the magnetic field will cause changes in the resistance value of the magnetoresistive sensor.
The above article briefly describes the principle of IMU. The MEMS IMU developed by ERICCO has the advantages of low cost, low consumption, high performance and light weight. It is very popular among customers. If you want to buy an IMU, please contact our professionals.
More Technical Questions
1.IMU working principle & Tactical grade IMU product recommendations
2.Choosing an IMU: FOG IMUs vs MEMS IMUs
3.Application of IMU in the Field of Drones
5.What is the Difference Between IMU and AHRS?
Products in Article
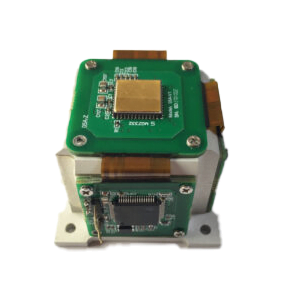
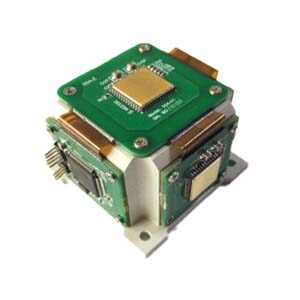
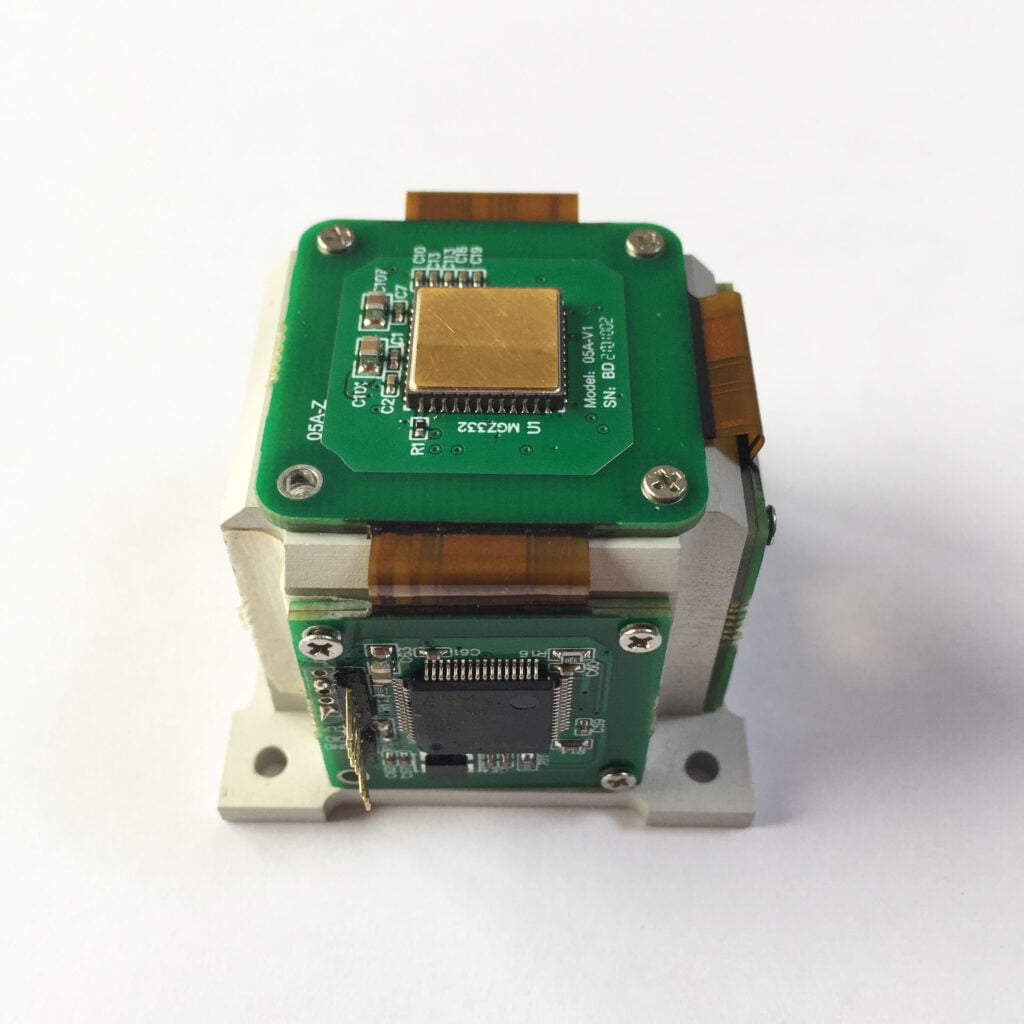
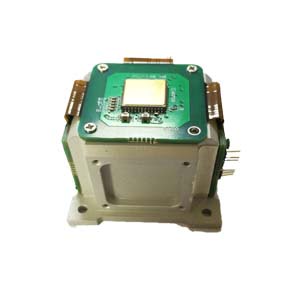
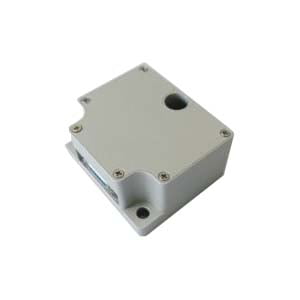
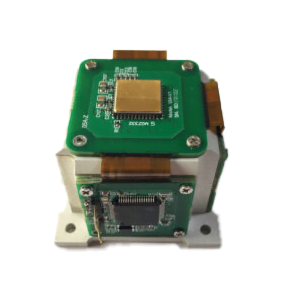