Now let's introduce the industry knowledge about accelerometers.
Whether in consumer electronics, industrial automation or automotive applications, when monitoring the running status and health status of the equipment, it is necessary to select the appropriate sensor according to the operation scenario of the equipment, to ensure that the sensor can accurately obtain the information of the equipment, and detect, diagnose and even predict the fault.
Vibration detection is a practical measurement method. The detected vibration data is the key predictive variable for fault diagnosis. Accelerometer is a commonly used sensor for vibration detection, widely used in consumer electronics, industrial automation, automotive sensing and other fields, it can collect state information for a single device or the whole system, and then provide sensor data to facilitate the system to predict the state of the device or system.
There are two main types of accelerometers to choose from, capacitive and piezoelectric. Thermal accelerometers are also available, but they are used less often in practical applications that we are familiar with and will not be listed separately here.
The capacitive accelerometer is based on the principle of capacitance pole distance change. In vibration, the capacitance pole distance changes, and then the capacitance value changes, so as to measure the acceleration value. In practice, to capture this sometimes tiny signal, a stack of capacitors is used to amplify it.
The piezoelectric accelerometer works on the piezoelectric effect, which is an effect in which the application of stress produces electric charge and the application of electric field produces dimensional deformation. In essence, it is a phenomenon of interaction between mechanical energy and electric energy. The piezoelectric effect applied to the sensor is the positive piezoelectric effect, that is, the conversion of mechanical energy into electrical energy, and the voltage value is proportional to the magnitude of the acceleration.
With the rapid development of sensors, MEMS accelerometer has become everyone's first choice. From the current products on the market, MEMS accelerometer basically takes a capacitive route. This is because the piezoelectric MEMS accelerometer is supported by rigid body inside. Usually, it can only sense the dynamic acceleration, but not the static acceleration, so the application is limited. Capacitive MEMS accelerometer can sense both dynamic acceleration and static acceleration.
However, from the development history of accelerometers, piezoelectric accelerometers are more widely used because of their good linearity, excellent dynamic range, high temperature operating characteristics and high bandwidth up to hundreds of kHz. For extreme performance, piezoelectric bandwidth and noise performance are certainly better, but also more expensive. In special cases where capacitive or capacitive MEMS accelerometers do not meet the performance requirements, piezoelectric route is a good choice.
With the support of MEMS, capacitive accelerometers are getting better and better in terms of small size, low power consumption and faster frequency response. Under the support of MEMS, the device can not only provide DC response, but also realize self-test under the support of ADC and tuned filter, which has attracted much attention in vibration detection.
Sensor selection in vibration detection
It can be clearly seen from the table above that the capacitive/capacitive MEMS accelerometer is more suitable for the measurement of low frequency vibration because of its low bandwidth, such as mobile phones, PCS and other mobile devices. The piezoelectric accelerometer can achieve the extreme high bandwidth, and is more suitable for the measurement of high frequency vibration.
We take a typical wearable device as an example. When choosing acceleration timing for vibration detection, wearable devices value low power consumption, small size and integrated features that can enhance energy-saving performance. Low power consumption is always a core indicator of wearable devices, and size and integration are also hard indicators in wearable devices.
This requirement limits the vibration detection can only choose capacitive MEMS accelerometer to detect motion and static acceleration. This kind of application does not have a high requirement on bandwidth, more than ten kHz to dozens of kHz, the requirement range of g value is usually around 1g. Capacitive MEMS accelerometers are well suited for this application, with the caveat that the device bandwidth and sampling rate may drop at low power to levels where available acceleration data cannot be measured.
This kind of vibration sensing can be seen everywhere in the industrial field, here take motor detection as an example. Vibration sensing in motor detection can generally be used to detect the following faults, bearing state, gear meshing, pump cavitation, motor misalignment, motor unbalance and motor load conditions. For unbalance, not aligned to this kind of fault, the noise performance requirements of the sensor parts is not strict, the bandwidth requirements also only need to reach 5× 10× fundamental frequency can, more requirements is that the sensor can detect multi-axis at the same time; Bearing defects and gear defects such as the fault on the noise and bandwidth requirements are very high, the noise range must be controlled in "100µg /√Hz, at the same time bandwidth requirements" 5kHz. In this case, the choice between capacitive and piezoelectric is very subtle. If the dynamic range of the scene is not very high and the bandwidth requirement is not high, the piezoelectric type will not be chosen when the capacitive accelerometer can be selected.
This is also a common option in the current trend of reducing wiring and power consumption in industrial wireless sensor networks, but only if the scenario conditions are favorable enough to accept lower accuracy data. In applications requiring high dynamic range, wide bandwidth, or extreme temperatures, piezoelectric accelerometers will undoubtedly be used. The use of piezoelectric accelerometers requires attention to minimize the sensitivity to external noise and crosstalk.
Global accelerometer sensor development
According to data compiled by QYResearch, from 2016 to 2020, the global accelerometer market size reached $2.057 billion at a compound annual growth rate of 2.28%. The global market size is expected to reach $2.162 billion in 2021 and $2.798 billion in 2027.
The scale of the Chinese market is also growing rapidly, which is expected to grow from $378 million in 2020 to $579 million in 2027. The capacitive MEMS accelerometer occupies the vast majority of the growth. The smaller size and higher integration of MEMS capacitive accelerometer is undoubtedly more in line with the development trend of sensors in all walks of life. Inadequate integration features can cause the accelerometer to be awkward in a cluster of sensor devices.
Most MEMS accelerometers are ADC integrated, but some can achieve higher bandwidth performance without ADC and then use an external ADC to ensure performance, either way seamlessly integrated with the sensor system. Power consumption needless to say, the current capacitive MEMS accelerometer power consumption control in µA, even nA range is available.
Ericco is a manufacturer of inertial products, accelerometers mainly producing quartz (flexure) accelerometers and MEMS accelerometers. Quartz accelerometer is also one of Ericco's hot selling products. If you want to know more technical data and quotation, please feel free to contact us.
More Technical Questions
1.Quartz Accelerometer VS MEMS Accelerometer
2.Why do we Need Accelerometer?
3.What are the Advantages and Disadvantages of Quartz Accelerometers?
4.What Effect Does Temperature Have on Quartz Flexible Accelerometer?
5.What is Sensitivity and Measurement Range in Quartz Accelerometer?
6.How to Improve the Long-term Stability of the Quartz Accelerometer?
Products in Article
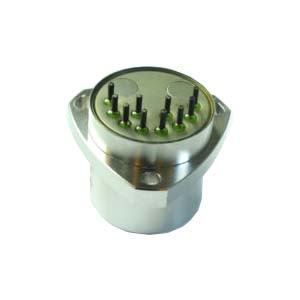
High Performance Quartz Accelerometer
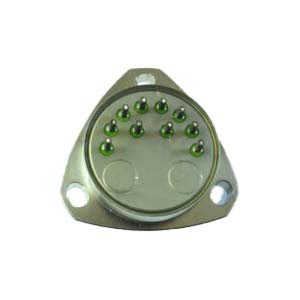
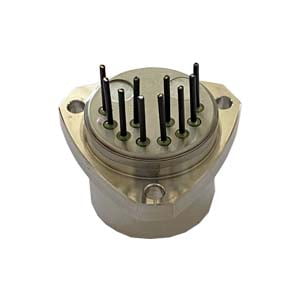
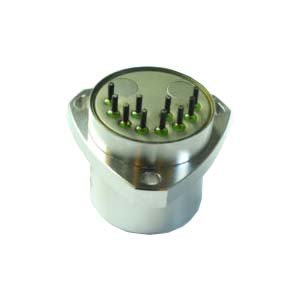
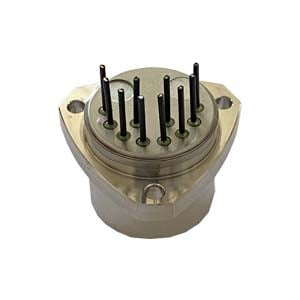
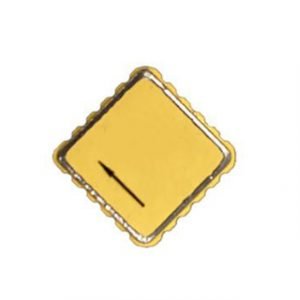