When it comes to indoor navigation and dealing with complex and environmentally challenging scenarios, sensors can be used to improve the system's ability to determine actual motion from abnormal motion.
Navigation is usually associated with cars, planes and ships. However, precision navigation is becoming more widely used in industrial and medical applications ranging from factory machinery and surgical robots to tracking by first responders. There are many existing methods to derive position, direction, and motion as they relate to pointing, steering, and guiding devices. In fact, it has become common for many applications to rely on GPS (Global Positioning System). But when it comes to navigating indoors and dealing with more complex and environmentally challenging scenarios, GPS alone is not enough.
For these types of applications, various sensor types can be used to improve the system's ability to determine actual motion from abnormal motion. The ability of a given sensor to solve a particular navigation problem depends not only on the performance level of the sensor, but also on the unique dynamics of the application. As with any complex design problem, the starting point is to understand the goals and limitations of the final application. From there, key performance parameters can be ranked to get a rough idea of the desired sensor, followed by actual design optimization through careful sensor conditioning, integration, and handling.
Understand navigation problems
Let's start with an analogy: Let's say you're at work and want a cup of coffee, so you navigate to the coffee pot. If you've been there before, you'll think of a route, but along the way you rely on all your senses to get there, including sight, audio, balance, and even touch. Your own personal processor combines these different sources, as well as some embedded pattern recognition, and if it's a tough day, you may need to pause and ask for some external input, namely directions. Throughout the process, you rely on your personal sensors not only to be precise alone, but also to work well together, to reject misleading information when necessary (i.e. the smell of coffee in your neighbor's cubicle), and to rely on other sensors. To get there, you need to employ the same techniques as designers of vehicles, surgical instruments, and robotic mechanical navigation systems.
Sensor selection and processing
Most solutions to all but the simplest problems rely on multiple sensor types in order to provide the desired accuracy and performance in all conditions. Inertial sensors, such as microelectromechanical systems (MEMS) -based accelerometers and gyroscopes, offer the potential to fully compensate for the shortcomings of other sensor types because they are not subject to many of the same interference and do not require external infrastructure (no satellites, no magnetic fields, no cameras...... Just inertia).
MEMS inertial sensors are highly reliable (with a 20-year track record in the automotive industry) and commercially attractive with lower power consumption, size and cost, as demonstrated by successful applications in mobile phones and video games. However, the level of performance available varies widely, and devices suitable for gaming cannot solve the high performance navigation problems outlined earlier. For example, precision industrial and medical navigation typically requires an order of magnitude higher performance level than the MEMS sensors used in consumer devices.
In most cases, the motion of the device is relatively complex (multiple axes), which drives the need for a full inertial measurement unit (IMUs) that can integrate up to six degrees of inertial motion freedom - three linear and three rotational.
As mentioned earlier, any sensor type has limitations, and if these limitations would compromise system performance goals, designers may choose to implement compensation techniques simultaneously and incorporate multiple sensor types. For example, an inertial measurement unit outputs highly stable linear and rotating sensor values that must compensate for the following effects:
Temperature and voltage drift
Bias, sensitivity, and nonlinearity
vibration
The X, Y, and Z axes are not aligned
Inertial sensors may have varying degrees of drift, depending on their mass, and this drift can be corrected occasionally using GPS or magnetometers. In addition to good sensor design, a central challenge in navigation is determining which sensors to rely on and when. Inertial MEMS accelerometers and gyroscopes have proven to be good additions to help designers design fully functional sensing systems.
The MEMS inertial sensor was used for the design
In indoor industrial or medical environments where GPS signals are rejected and mechanical and electronic devices introduce magnetic interference, designers must establish less traditional methods of machine guidance. Many emerging applications, such as surgical tool navigation, also require greater accuracy than car navigation. In all of these cases, inertial sensors are an option and provide dead reckoning guidance needed to maintain accuracy during line of sight blocking or other sources of interference harmful to non-inertial sensors.
In addition to better alignment for increased comfort and faster, less invasive surgical targets, the right sensors can help combat hand tremors and fatigue. In recent years, pure mechanical alignment has been supplemented by optical alignment, but like GPS blocking for vehicle navigation, there is potential line of sight blocking in the operating room that limits the accuracy of optical sensors. Inertially guided surgical alignment tools can complement or even replace optical guidance, without line-of-sight problems, and have potential advantages in terms of size, cost, and automation.
Although the basics of solving navigation problems are very consistent from application to application, the details of the terminal system must be fully understood. These ultimately guide the selection of the appropriate sensor type and overall performance.
While there is a strong push for small, low-power, multi-axis inertial sensors for consumer applications, some sensor developers are equally highly focused on the high accuracy of compact, low-power, high-performance sensors in all conditions. These high-precision, environmentally robust sensor developments are driving a new wave of adoption of MEMS inertial sensors in the industrial, instrumentation, and medical markets.
Ericco is a manufacturer of mems inertial sensors. We provide navigation level mems sensors and north-seeking level mems sensors. If you want to obtain more technical data, you can contact us at any time.
More Technical Questions
1.Application of MEMS Sensors in Aerospace Equipment
2.Introduction to MEMS Sensors
3.Precision MEMS Sensors Realize New Navigation Applications
4.The Development Potential of MEMS Sensors
5.Applications of MEMS Sensors
6.MEMS Sensors Welding Process
Products in Article
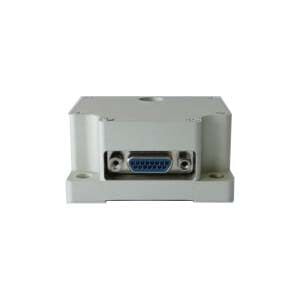
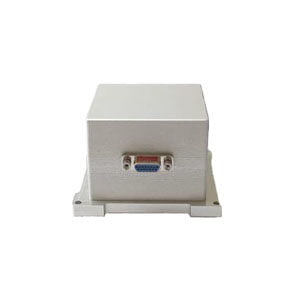
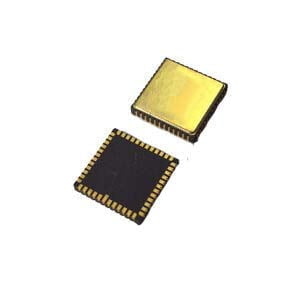
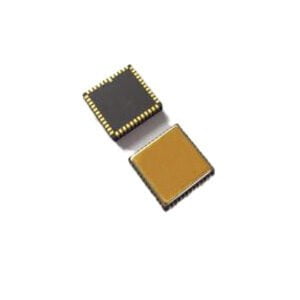
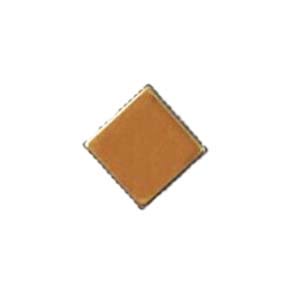
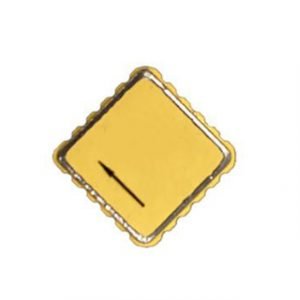