MWD(Measurement While Drilling) refers to the continuous testing of information about the Drilling hole or bit by the Drilling rig While Drilling. MWD is the process by which certain information is measured near the bit and transmitted to the surface without interrupting normal drilling operations.
Types of information:
(1) directional data (inclination, azimuth, tool face Angle);
(2) Formation characteristics (gamma ray, resistivity logging);
(3) Drilling parameters (weight on bit, torque, revolution).
The sensors are housed in special downhole instruments that are part of the entire BHA. There is a transmitter in the downhole instrument that sends the signal to the surface via some kind of telemetry channel. The most common telemetry channel used today is the drilling fluid column within the drilling string. After the signal is detected on the ground, it is decoded and processed to provide the required information in a convenient and usable manner. The biggest advantage of MWD is that it can "see" what is happening in the borehole in real time, improving the decision making process by delaying measurements from the bottom of the borehole to the surface in just a few minutes.
MWD means that the rig continuously and continuously detects information about the drill or drill bit while drilling, and is realized by the tracking and guiding instrument. Therefore, the tracking and guiding instrument is necessary for horizontal directional drilling machine construction. Measuring equipment. LWD (Logging While Drilling) is based on MWD , adding several parameter sensors for formation evaluation, such as compensating for dual lateral resistivity, natural gamma, Azimuth neutron density, sound waves, and compensated neutron density have been developed.
The methods to realize MWD telemetry include hard wire method, electromagnetic wave method, acoustic wave method and drilling fluid pulse method. At present, the drilling fluid pulse method is widely used, and the pressure pulse is transmitted to the surface through the fluid column in the drill pipe at the speed of 1200 ~ 1500m/s. All downhole components are housed in non-magnetic drill collars. Because the components of the MWD tool are to be accommodated, the bore diameter is larger than that of ordinary drill collars. The ER-MWD-38 small diameter measuring instrument for drilling holes has an outer diameter of 38mm. In the small hole construction, the hole of the non-magnetic drill tool can not be reamed. When used in the conventional large hole construction, the mud and water circulation area of the non-magnetic drill collar is relatively increased, reducing the erosion of the drilling equipment and the drill tool, which is conducive to the safe construction of the well team because of the characteristics of high precision, high stability and high vibration resistance, and has a wider range of applications.
Characteristic
There is a downhole controller in the MWD downhole instrument, which is a downhole CPU composed of a single board mechanism, and its role is to coordinate and control various work sequences of the MWD instrument. The downhole controller converts the parameters measured by various downhole sensors into electrical signals, and then directs the pulse generator to convert these signals into drilling fluid pulse signals in a specific sequence and format (code), and sends them upward through the drilling fluid column in the drill pipe to the ground sensor, signal decoding and data processing system, and carries out signal pickup, conversion, decoding and processing for the operator Line analysis decision.
Common MWD is mainly to measure the well track parameters, namely the inclination and azimuth, and the tool face Angle (ω) when sliding drilling with downhole power drilling tools. Sensors that measure these engineering parameters are also called orientation sensors.
If you want to get more details about MWD,pls visit https://www.ericcointernational.com/north-finding-system/mwd
More Technical Questions
1.Development of MWD for Directional Drilling
2.GWD – Gyro-while-drilling Technology Superior to Traditional MWD
3.What Is The Difference Between MWD And LWD?
4.What Is The Principle Of MWD?
5.Possible Problems And Solutions For Shallow Testing Of MWD Instruments
6.Wireless Transmission of MWD and LWD
Products in Article
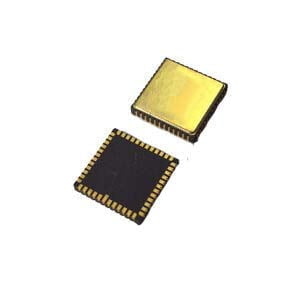
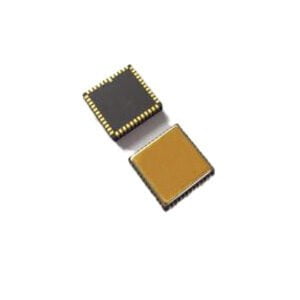
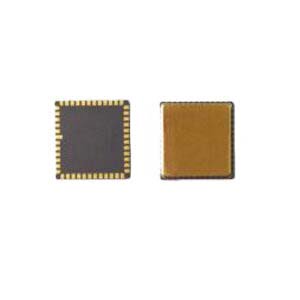
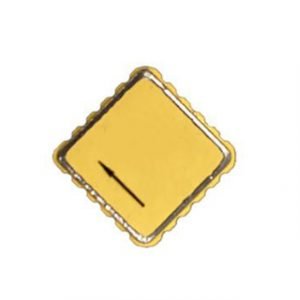
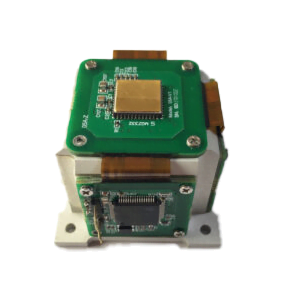