Apply MEMS IMU attitude measuring on a tactical level project, in more complex and practical circumstances, MEMS IMU and MEMS inertial sensors in the corresponding compensation needs to be done. Because of MEMS inertial sensor which made MEMS IMU works very different from other types of sensors, therefore to carry out the error of MEMS inertial sensors under the experimental condition of mechanism, it is the basis of compensation method.
First of all, the analysis of a tactical level precision MEMS - the error of IMU prototype, including MEMS inertial sensor error produced and integration, assessed under the experimental conditions for calculating the error caused by the navigation error of size, the research is focused on sensor sensitivity temperature drift error and acceleration error suppression. Then, put forward to analyze statistical parameters of micro structure error caused by output error method, established the micro sensor output error and error of the size of the manufacturing process. It can be used to predict a given manufacturing process under the condition of the error of the sensor can achieve targets. Then, on the basis of considering processing steps, analyzes several kinds of micro accelerometer temperature drift possible reasons, mainly analyzes silicon glass relative displacement caused by thermal expansion coefficient mismatch, and micro accelerometer machining error caused by the u-shaped girder stiffness asymmetry synthesis of contribution, and the temperature drift of analytic calculation; Set up the structure of micro accelerometer - electrostatic - temperature physical field coupling finite element model and the simulation analysis of temperature drift, also the temperature experiments, and the analysis, simulation and experimental results are compared.
Then, analyzes the bipolar decoupling micro gyroscope acceleration sensitivity and temperature drift possible reasons.Micro gyroscope structure finite element model is established, the sensitivity of the micro gyro temperature drift and acceleration simulation results, and then through the temperature experiment and centrifugal experiment analysis of the error term, comparing simulation and experimental results verified.
Finally, the experimental researches on specific problems in the use. It proposes a MEMS IMU machine calibration compensation method. Put forward to using the magnetic field sensor measurement range over micro gyroscope angular rate method.
Ericco’s MEMS IMU ER-MIMU-03 and ER-MIMU-07 use MEMS accelerometer and gyroscope with high quality and reliability, RS422 and external communication, baud rate can be flexibly set between 9600~921600, through the communication protocol to set the user’s required communication baud rate. With X, Y, Z three-axis precision gyro, X, Y, Z three-axis accelerometer with high resolution, can be output by RS422 X, Y, Z three axis of gyroscope and accelerometer’s original hexadecimal complement data (including gyro hexadecimal complement the numerical temperature, angle, the accelerometer hexadecimal temperature, the acceleration hexadecimal complement number); It can also output float dimensionless values of the gyroscope and accelerometer processed by the underlying calculation.
If you are interested in MEMS IMU ER-MIMU-03 and ER-MIMU-07 for more product information, please contact us: info@ericcointernational.com
More Technical Questions
1.Research Background and Current Status of MEMS IMU
2.What are the advantages of MEMS IMU?
3.IMU in Drones (MEMS triaxial accelerometer, triaxial gyroscope, triaxial magnetometer)
5.IMU Based on MEMS Technology
Products in Article
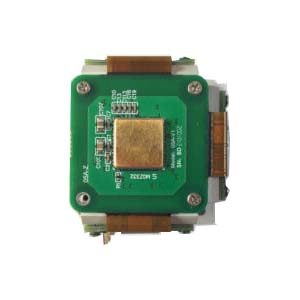

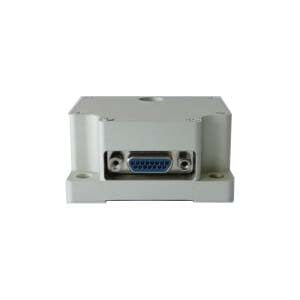
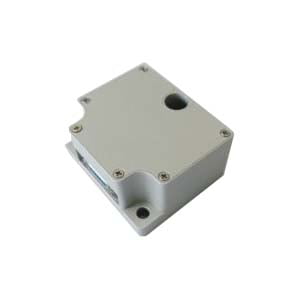
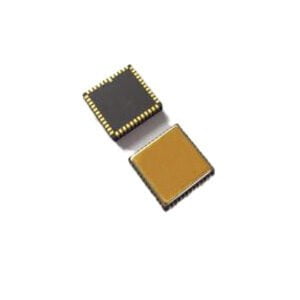
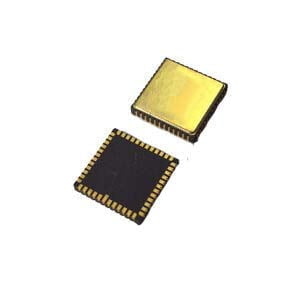