With the rapid development of UAV technology, the requirements of flight control system for accuracy, reliability and environmental adaptability are increasingly stringent. With its excellent performance parameters and compact design, the ER-3MG-07 series three-axis MEMS gyroscope is becoming a key component in the UAV field to improve flight stability, navigation accuracy and mission execution.
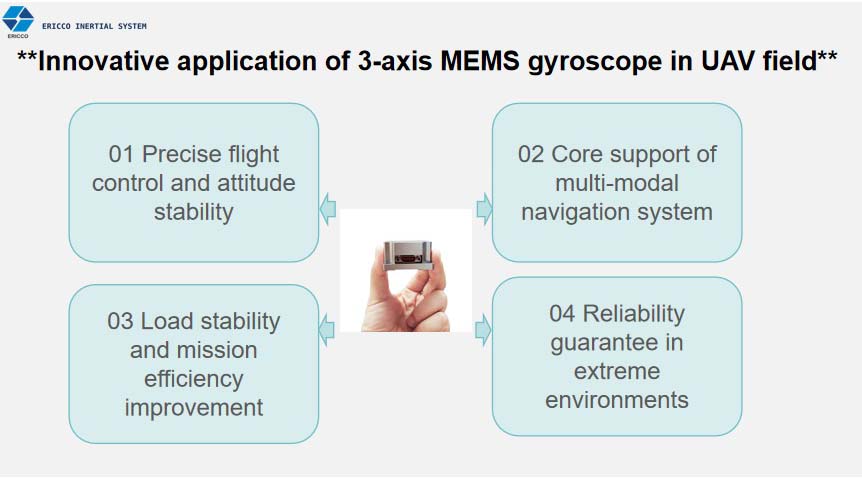
**Precise flight control and attitude stability**
The flight stability of UAV directly depends on its attitude perception ability. The ER-3MG-07 series gyroscope provides high dynamic response data to the flight control system by measuring the triaxial angular velocity in real time (range ±400°/s). Its bias instability of <0.1 deg/hr and angular random walk characteristic of <0.05°/√h significantly reduce the attitude drift error in flight. For example, in the case of strong wind disturbances or high-speed maneuvers, the sensor's high-frequency response capability (10s bias stability <1 deg/hr) can quickly correct the flight attitude and avoid the risk of loss of control due to data delay.
**Core support of multi-modal navigation system**
In complex environments, such as urban canyons or areas without GPS signals, drones rely on inertial navigation systems (INS) for autonomous positioning. The ER-3MG-07's 20000 LSB/deg/s high sensitivity (B/C model) and <300 ppm nonlinear error ensure a high linearity output of the angular velocity signal, which can be accurately calculated when combined with the accelerometer data. The 300 ppm temperature drift suppression capability, combined with a wide temperature operating range of -45 ° C to +85 ° C, ensures navigation reliability in extremely cold or high temperature environments. For example, in agricultural plant protection drone operations, our three-axis gyroscope can assist in centimeter-level course tracking to avoid respray or missing spray problems.
**Load stability and mission efficiency improvement**
The loads such as photoelectric pods and lidar carried by UAVs require very high stability of the platform. ER-3MG-07 drives the Pinion servo system for reverse compensation through real-time feedback of the body angular motion, and its scale factor repeatability of <50 ppm significantly improves the Pinion control accuracy. Taking film and television aerial shooting as an example, the high-frequency noise suppression ability of the gyroscope (ARW<0.05°/√h) can greatly reduce the high-frequency jitter of the video picture, and the movie-level stability effect can be achieved with the PTZ algorithm. In mapping drones, the technology can ensure the geometric consistency of laser scanning point clouds and improve the accuracy of three-dimensional modeling.
**Reliability guarantee in extreme environments**
The outdoor operation of drones often faces severe temperature differences, vibration and electromagnetic interference. ER-3MG-07 uses MEMS process and all-solid-state design to avoid the complex optical structure of traditional fiber optic gyroscope and has stronger impact resistance (through military-grade reliability verification). Its storage temperature range of -55 ° C to +105 ° C can adapt to the transportation and deployment needs of extreme climates such as deserts and polar regions. For example, in the power inspection scenario, the UAV needs to pass through the high-voltage electric field in the low temperature in winter, and the stable output of the sensor can ensure the safety and reliability of the inspection path.
Summary
The ER-3MG-07 series MEMS gyroscope redefines the technological boundaries of UAV sensors through breakthrough performance indicators and engineering design. From consumer aerial photography to industrial inspection, from stand-alone operation to intelligent clustering, this three-axis MEMS gyroscope is becoming the core technology for high-precision, high-reliability and all-weather operation of drones. With the continuous iteration of MEMS processes, its cost advantages and mass production capabilities will further promote the inclusive and professional development of the UAV industry.
Application Techniques
1.Main features of MEMS gyroscope
2.Sensitive structure analysis of MEMS gyroscope
3.The analysis of damping in MEMS gyroscope
4.The impact of turntable error on MEMS gyroscope calibration
5.How does MEMS gyroscope work in harsh high temperature environment?
6.Error Generation Mechanism of MEMS Gyroscope Under High Acceleration Condition