The MEMS IMU ER-MIMU-17, based on micro-electromechanical systems (MEMS) technology, integrates a three-axis gyroscope and a three-axis accelerometer, capable of real-time monitoring of three-axis angular velocity and acceleration. Although it may not be the top performer in terms of precision within the industry, it stands out with its high cost-effectiveness and excellent stability, making it a reliable assistant in numerous industrial scenarios.
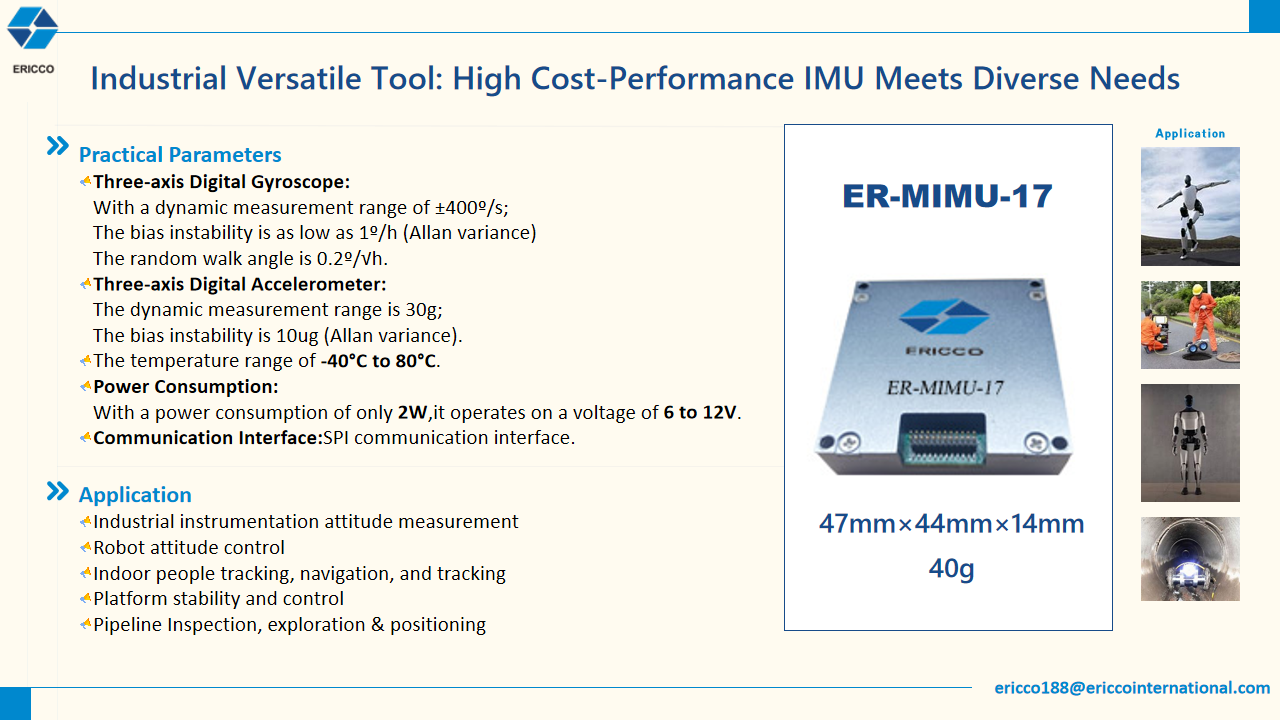
Practical Parameters
- Three-axis Gyroscope: With a dynamic measurement range of ±400º/s, it can meet the routine rotation and steering measurement requirements of equipment; the bias instability is as low as 1º/h (Allan variance), and the random walk angle is 0.2º/√h, ensuring relatively stable accuracy during continuous measurement.
- Three-axis Accelerometer: The dynamic measurement range is 30g, capable of sensing common acceleration and deceleration changes in equipment; the bias instability is 10ug (Allan variance), and with built-in temperature calibration and compensation algorithms, it ensures that measurement data is not significantly affected within the temperature range of -40°C to 80°C.
- Power Consumption and Compatibility: With a power consumption of only 2W, it is energy-efficient and reduces the heat dissipation pressure on the equipment; it operates on a voltage of 6 to 12V, compatible with various power sources; its dimensions are 47×44×14mm, weighing 40g, making it compact and lightweight, and easy to integrate into various devices.
- Communication Interface: It features one SPI communication interface, ensuring efficient and stable data transmission, facilitating the construction of automated systems with other devices.
In various industrial applications, the ER-MIMU-17 demonstrates strong practicality and adaptability.
Whether it is assisting in fine-tuning parameters of industrial control systems to ensure stable and efficient production processes, or playing a key role in the posture control of industrial robots, it can complete tasks with reasonable precision, enhancing overall operational efficiency. Additionally, in scenarios with high stability requirements such as vehicles and lifting platforms, it can monitor the movement status of the platform in real time, helping the control system maintain stable operation and reduce the risk of accidents. Moreover, in pipeline inspection work, it can assist in the positioning and posture perception of inspection equipment, providing accurate information to workers and accelerating problem detection.
The ER-MIMU-17, with its practical performance, is a cost-effective choice for industrial measurement. If your project does not have extremely strict precision requirements but values stability, cost, and applicability, it would be an excellent option, injecting stable power into your industrial production.
More Technical Questions
1.IMU working principle & Tactical grade IMU product recommendations
2.Choosing an IMU: FOG IMUs vs MEMS IMUs
3.Application of IMU in the Field of Drones
5.What is the Difference Between IMU and AHRS?