The theoretical basis is Newton's second law: according to the basic physical principles, within a system, the speed is not measurable, but its acceleration can be measured. If the initial velocity is known, the linear velocity can be calculated by integration, and then the linear displacement can be calculated, so it is actually an acceleration sensor using the principle of inertia.
When the tilt sensor is stationary, that is, there is no acceleration in the side and vertical directions, then only the gravitational acceleration acts on it. The angle between the vertical axis of gravity and the sensitive axis of the acceleration sensor is the angle of inclination. In general, the tilt sensor is a static measurement or a quasi-static measurement. Once there is external acceleration, the acceleration measured by the acceleration chip contains the external acceleration, so the calculated angle is not accurate. Therefore, the common practice now is to increase the mems. Gyro chip, and uses the preferred Kalman filter algorithm. Acceleration 3 axes, gyroscope 3 axes, all products here are also called 6-axis or VG (vertical gyro).Inclination sensors are generally divided into two types: single-axis inclination sensors and dual-axis inclination sensors. A uniaxial tilt sensor can only measure the tilt Angle of an object along one axis, while a biaxial tilt sensor can simultaneously measure the tilt Angle of an object along two axes.
Application field:
Bridge safety monitoring
In the bridge health monitoring system, there are environmental monitoring, deformation monitoring, stress and strain monitoring, and bridge deck load monitoring. Among the many physical quantities to be measured, it is necessary to use the inclination sensor to measure the slight change of the tilt Angle of the bridge. Inclination sensors are usually placed on the deck and tower to measure the deformation of the bridge under load and to evaluate the structural integrity and stability of the bridge, respectively. The bridge tower is another place that needs to be measured by inclination sensor. The inclination value of the bridge tower reflects whether the integrity and stability of the bridge structure are affected to a certain extent, and whether it will endanger the safety of the bridge.
Rotary drilling rig operation
The position of the center of gravity in rotary drilling rig is the key factor affecting the stability of rotary drilling rig. There are many factors that affect the center of gravity position of rotary drilling machine. The static factors include the Angle between chassis and horizontal plane, the position of amplitude changing mechanism, the inclination of mast, the weight of each component of drilling machine, etc. Dynamic factors include pressure, lifting force, turning speed, etc. When calculating the center of the rotary drilling rig, the rotation center of the rotary drilling rig is taken as the coordinate origin, and the inclination sensor on the rotary drilling rig is used to measure the inclination degree of the corresponding components, so as to calculate the center of gravity position of each component, and then combined with the weight of each component, the static center of gravity coordinates of the rotary drilling rig can be determined. In addition, the attitude of the drill bit determines the success or failure of the drilling process. The inclination sensor is installed inside the drill bit to detect the attitude of the drill bit in real time, or to measure it when it is stopped.
Aerial work monitoring
When working at altitude, it is very important for the safety of altitude workers to ensure that the bottom plane of the platform is always level. At this time, it is necessary to use the inclination module to monitor the inclination Angle of the equipment in real time and accurately.
For example, an inclination sensor is installed on the platform chassis of the aerial work vehicle to detect the tilt state of the chassis. Once the tilt is too large, the tilt sensor will automatically alarm to prevent tipping. Another example is the installation of tilt switches on the shear and fork aerial work platform to automate, highly reliable, real-time Angle measurement, control and alarm of the operating platform and the entire equipment.
More Technical Questions
1.Application of Inclination Sensor in Electronic Belt Conveyor
2.The Difference and Application of Single and Dual Axis Inclination Sensors
3.Composition and Application of Inclination Sensor
4.How accurate is MEMS gyroscope?
5.Inclination Sensor Principle
6.How to Use Acquisition Software of MEMS North Seeker
Products in Article
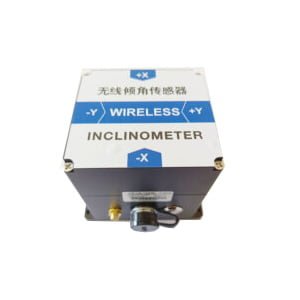

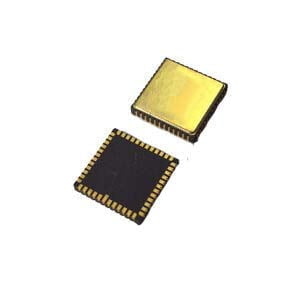
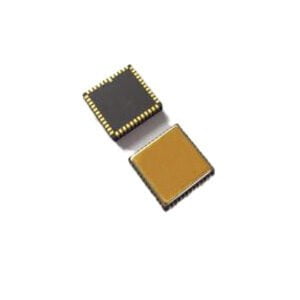
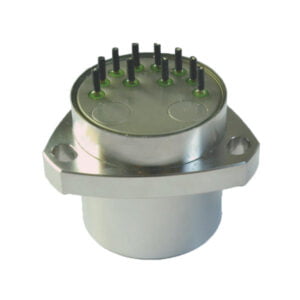
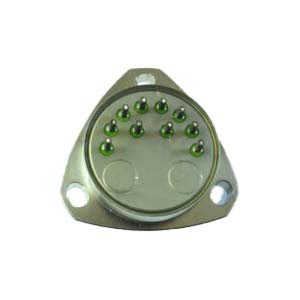