Many people don't know how to choose cost-effective and suitable inertial products when they first come into contact with them. They often lack an understanding of important parameters and make the wrong choice. Today, I will first introduce you to the classification of inertial product levels, and take the gyroscope as an example to introduce how to choose a gyroscope.
Performance classification
In general, inertial sensors are divided into the following three levels:
A. Navigational level: Large, Accurate and Expensive
Marine-class inertial navigation systems are the highest level of commercially available sensors, used on ships, submarines, and occasionally on spacecraft. The system can provide an unassisted navigation solution with a drift of less than 1.8km/day. These sensors cost up to $1 million.
The performance of the navigation-level inertial navigation system is slightly lower than that of the marine-grade inertial navigation system, and is usually used in commercial airliners and military aircraft. Its drift is less than 1.5km/h, and its price is as high as $100,000.
B. Tactical and Industrial level: High Value for Mainstream Applications
Tactical-grade and industrial-grade sensors are the most diverse of the three categories, addressing a variety of performance and cost scenarios, and the market opportunity is enormous. This category is used in many applications that require high-performance data at low cost for mass production, commonly found in mining, drilling, delivery robots, drones, agriculture, and autonomous ships. While the price is lower, buyers can get cost-effective products with good accuracy, performance, size and quality. Our ER-MG2-100 for north seeking is at the top of the tactical level, which bias stability is only 0.1°/h. And our ER-MG2-400 for navigation is also with high performance, which bias stability is 0.5°/h.
C. Automotive-level and Consumer-level: Commodity Applications
In the commercial market, the lowest level of sensors is called the automotive level. These sensors are usually sold as separate accelerometers or gyroscopes. Many companies have started combining multiple accelerometers and gyroscopes from different manufacturers to create independent IMU units. Even when integrated with other navigation systems such as GPS, automotive-level IMUs are not accurate enough for inertial navigation. These sensors are commonly used in suspension systems, airbags, anti-lock braking systems, entertainment systems and other similar applications.
Selection of gyroscope
Here are some indicators to pay attention to in the selection process of a gyroscope:
Range
The range is the first thing we need to determine when selecting a sensor. The maximum value of the input angular rate in the forward and reverse directions of the gyroscope represents the measurement range of the gyroscope. The larger the value, the stronger the sensitivity rate of the gyroscope. The unit is °/sec. For general flight control, the inertial navigation system can be selected at 300 °/s and 450 °/s, and the others can be selected according to their own usage scenarios. For example, a smaller range gives a higher resolution and is suitable for directional north-seeking.
Sensitivity
Indicates the increment of the minimum input angular rate that can be sensed at the specified input angular rate. Smaller means better. When selecting, the appropriate measurement range must be selected for different applications. Because the measurement range is large, the sensitivity will be correspondingly reduced.
Nonlinearity
Scale factor: The ratio of the gyroscope output to the input angular rate, which is the slope of the straight line obtained by least squares fitting based on the input/output data measured in the entire input angular rate range.
The residual error of the scale factor fitting determines the credibility of the fitted data and represents the deviation of the actual input/output data of the gyro. The nonlinearity of 0.1% of the full scale refers to the nonlinearity of the scale factor.
Initial bias error
Bias refers to the output of the gyroscope in the zero input state, which is expressed by equivalently converting the mean value of the output for a long time to the input angular rate, that is, the degree of dispersion of the observation value around the zero bias, such as 0.05 °/hr means drift 0.05 degree per hour.
Bias stability
The long-term steady-state output in the zero-input state is a stationary random process, that is, the steady-state output will fluctuate and fluctuate around the mean (zero-bias), which is customarily represented by the mean square error, which is defined as the zero-bias stability. The initial zero bias error can be understood as a static error, which does not fluctuate with time and can be calibrated by software.
The following table lists the approximate range of key parameters of gyroscopes for different grades of use:
Parameter | Navigation level | Tactical level | Consumer level |
Scale factor stability(ppm) | 1-100 | 100-1000 | >1000 |
Bias stability(°/h) | 0.01-0.09 | 0.10-15 | >15 |
Angular Random Walk(°/√h) | 0.01-0.05 | 0.05-0.5 | >0.5 |
Output noise
When the gyro is in the zero input state, the output signal of the gyro is the superposition of white noise and slowly varying random functions. Its slowly varying random function can be used to determine the zero bias or zero bias stability index. White noise is defined as the standard deviation of the equivalent rotational angular rate under the square root of the unit detection bandwidth, in units (°/sec)/√HZ or (°/hr) /√Hz. This white noise can also be represented by an angle random walk coefficient in units of °/√hr, which refers to the gyro output error coefficient accumulated at random time generated by white noise. When the external conditions are basically unchanged, it can be considered that the main statistical characteristics of the various noises analyzed above do not change with the passage of time.
Linear acceleration effect
In theory, the gyroscope only tests the rotational angular velocity, but in fact all gyroscopes are sensitive to acceleration, and the acceleration of gravity is ubiquitous, and in field applications, it is difficult to ensure that the gyroscope is not affected by the acceleration caused by shock and vibration, so that in practical applications, the sensitivity index of the gyro to acceleration is very important.
Bandwidth
The gyro can accurately measure the frequency range of the input angular rate. The larger the range, the stronger the dynamic response of the gyro.
Vibration resistance
For the performance parameters of the gyroscope, the first thing most designers should pay attention to is bias stability. It has been regarded as the absolute standard of gyroscope specification for a long time. After all, it is the lower limit of the resolution of the gyroscope, so it should be is the best indicator of responsive gyroscope performance! However, in practice, the gyroscope will have errors due to various reasons, so that the user cannot obtain the index parameters declared in the experimental manual. In fact, many performance parameters can be improved in subsequent calibration algorithms such as zero offset, scale factor, quadrature axis error, and temperature drift.
When choosing a gyroscope, you need to consider minimizing the largest source of error. In most applications, vibration sensitivity is the largest source of error. Other parameters can easily be improved by calibrating or averaging multiple sensors. Bias stability is one of the smaller components of the error budget.
In an ideal state, the gyroscope only needs to measure the rotation rate, but in practical applications, all gyroscopes have a certain acceleration sensitivity. Sensitivity or sensitivity to vibration (g2 sensitivity), since most gyroscope applications are in devices that move around and/or rotate in the Earth's 1g gravitational field, sensitivity to acceleration is often the largest error source.
Of course, in some practical applications, many people will add a mechanical anti-vibration component to the device, and the design of the anti-vibration component is not a simple matter, because its response in a wide frequency range is not flat, and at low frequencies, It is particularly poor, and its damping properties vary with temperature and time of use.
Therefore, in most applications, the vibration resistance is a very critical indicator in the selection process of the gyroscope.
For more product details or application knowledge, please feel free to visit our website.
More Technical Questions
1.What is the Difference between a Gyroscope sensor and an Acceleration Sensor?
2.What’s a Gyroscope do? You Can See that From the Application of the Balance Car
3.What Is The Functional Difference Between A Gyroscope And An Accelerometer?
4.What Is The Precession Of A Gyroscope?
5.What Is The Orientation Of A Gyroscope?
6.What Is The Difference Between An accelerometer And A Gyroscope
Products in Article
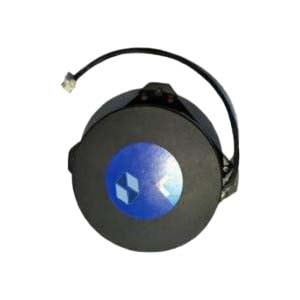
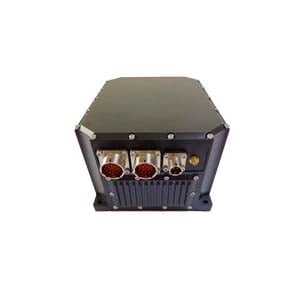
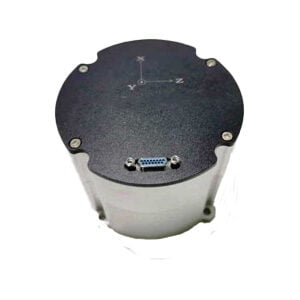
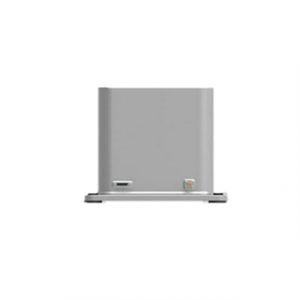
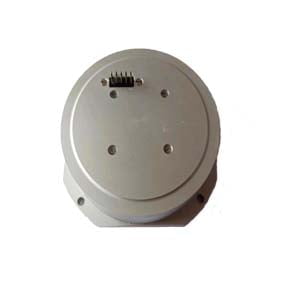
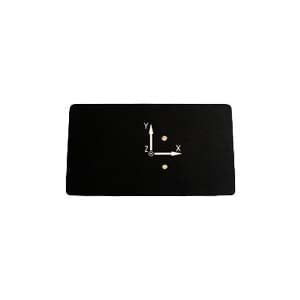