Accelerometer is the basic measurement element of inertial navigation and inertial guidance system. It is installed inside the projectile (rocket) to measure the motion acceleration of the projectile (rocket), and its speed and position are obtained by integrating the acceleration. Therefore, the performance and accuracy of the accelerometer directly affect the accuracy of the navigation and guidance system.
Quartz flexible accelerometer is actually a sensor that can accurately measure acceleration, and it is a member of the big family of accelerometers. The quartz flexible accelerometer is more accurate and can be used in a wider range of applications than a sensor called a MEMS accelerometer that you use in your mobile phone. Has been widely used in aerospace, aviation, ships, weapons, petroleum, geotechnical engineering and many other fields, for various systems of navigation, guidance, control, leveling, monitoring and so on to provide accurate acceleration measurement signals.ER-QA-03A High Performance Quartz Accelerometer with high reliability is mainly used in inertial measurement and test systems in the aerospace and aviation fields. It can carry out static test and dynamic test, which is a standard vibration sensor.
Quartz flexible accelerometer is a new high-precision solid state sensor based on the force frequency characteristics of quartz vibration beam. The vibration excitation circuit performs piezoelectric excitation on the quartz vibration beam to form bending vibration at the resonance frequency point, and the mass block converts the external input acceleration into the axial force acting on the vibration beam. According to the force-frequency characteristics of the beam, the resonant frequency of the beam is changed by changing the stiffness of the beam, and the magnitude and direction of the acceleration are obtained by detecting the frequency difference between the two beams.
Compared with the pendulum integrating gyro accelerometer and pendulum accelerometer, the quartz vibration beam accelerometer has fewer parts and lower power consumption. The sensitive structure has no other mechanical wear parts except for the weak vibration of the two resonant beams at the nanoscale, which also gives it a longer average failure time and higher reliability. The scale factor stability and axial positioning of vibrating beam accelerometers are particularly good, which is a direct result of the use of resonant force transducers. The scaling factor is determined by the quality and elastic constant of the quartz, and the positioning of the input axis mainly depends on the position of the pendulum, which is related to the inherent stability of the quartz. The very precise scale factor and good axial positioning performance are very useful in the inclination measurement of navigators, because it is to measure the component of the Earth's gravity.
The first hurdle in the quartz flexible accelerometer's journey into space was the big mechanical impact of launch. Quartz flexible accelerometers are tiny compared to big things like rockets, but it's their tiny size that gives them the advantage of high-precision measurements. It was also the precision of the measurement requirements, making the quartz flexible accelerometer "temperamental", appear hard to bear, in the process of rocket star arrow separation big impact, therefore need to quartz flexible accelerometer for special design, when large mechanical shock comes, can quickly to the impact of quartz flexible accelerometer is resolved.
Space travel is romantic, but as you get higher up, the air gets thinner and the atmospheric pressure gets lower and lower, and eventually you get close to a vacuum. In order to ensure the measurement accuracy of the quartz flexible accelerometer, the quartz flexible accelerometer must be sealed, that is, to put on a set of airtight "coat" to the quartz flexible accelerometer. In order to fully ensure the reliability of the seal, and simulate the use environment in space, the seal coat was subjected to severe tests such as vibration and impact. After being thoroughly tempered, the quartz flexible accelerometer seal coat finally came out, which provides a solid barrier for the quartz flexible accelerometer to work in vacuum environment.
All based on the simple, reliable, high-precision design idea, the "greenhouse" has carried out a lot of test verification and improvement, ultimately to ensure the "greenhouse" high precision constant temperature and ensure the high reliability.
More Technical Questions
1.Why do we Need Accelerometer?
2.What is the Purpose of the Accelerometer Senor?
3.Application of Quartz Accelerometer in UAV and Positioning System
4.What is the Purpose of the Accelerometer Senor?
5.What Effect Does Temperature Have on Quartz Flexible Accelerometer?
6.How do parameters affect the performance of the quartz accelerometer?
Products in Article
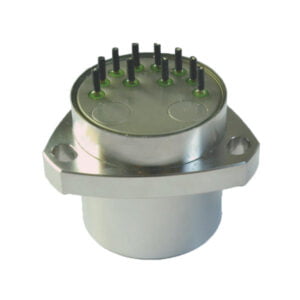
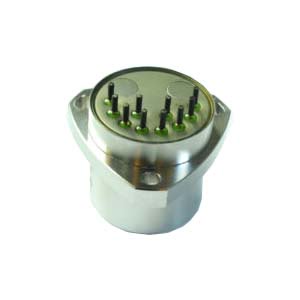
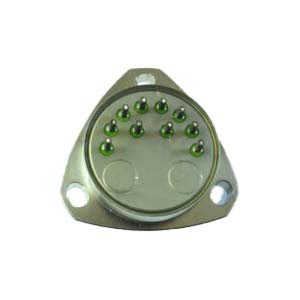
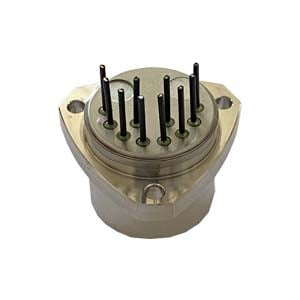
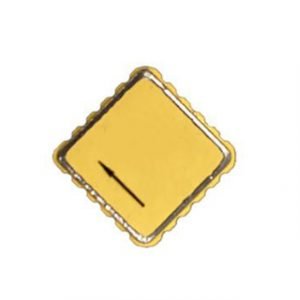
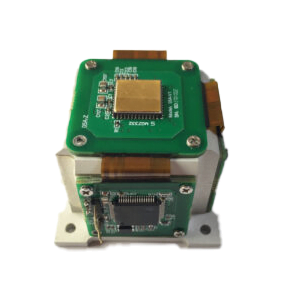