An accelerometer is an instrument that measures acceleration. Acceleration measurement is an important subject in engineering technology. When the object has a large acceleration, the object and the instruments and equipment carried by it and other objects without relative acceleration are subjected to forces that can produce the same large acceleration, that is, dynamic loads. To know the dynamic load, you need to measure the acceleration.
There are many types of accelerometers. Micro-mechanical accelerometers, also known as silicon accelerometers, are now widely used. The principle of sensing acceleration is the same as that of general accelerometers. According to the different reading elements, micro-mechanical accelerometers are classified into piezoresistive accelerometers, capacitive accelerometers, resonant beam accelerometers, and electrostatic force balanced accelerometers. The micro-mechanical accelerometer is small in size, easy to install, simple in measurement method, low in cost and strong in anti-overload capability, and satisfies the requirements for the structure and space limitation of the micro-mini aircraft.
Accelerometers consist of test masses (also called sensitive masses), supports, potentiometers, springs, dampers, and housings. The detected mass is constrained by the support and can only move along the axis, which is often called the input axis or the sensitive axis. According to the number of input shafts, there are single-axis, dual-axis and triaxial accelerometers.
With the development of MEMS technology, inertial sensor is one of the most widely used MEMS devices, and micro-accelerometer is an outstanding representative of inertial sensor. The theoretical basis of the microaccelerometer is Newton's second law, according to the basic principles of physics, within a system, the speed cannot be measured, but its acceleration can be measured. If the initial velocity is known, the linear velocity can be calculated by integrating, and the linear displacement can then be calculated. Combined with a gyroscope (used to measure angular velocity), the object can be precisely positioned. The high-precision MEMS accelerometer ER-MA-5 has a bias stability of 5 ug and a monthly bias repeatability of 100-300 ug.
Application
Car safety system
Accelerometers play an important role in automobile safety system. For example, when a car is in a collision, the accelerometer can detect changes in the vehicle's acceleration and send signals to the airbag system to inflate it at the appropriate time, protecting the driver and passengers. In addition, accelerometers can also be used in vehicle stability control systems to help vehicles in emergency situations. Keep it steady.
Aerospace
Accelerometers are also widely used in the aerospace field. During a rocket launch, for example, an accelerometer can measure changes in the rocket's acceleration to help control the trajectory of the rocket. In addition, the accelerometer can also be used in the aircraft's autopilot system to help maintain stability.For example, the ER-QA-03A accelerometers commonly used in the aerospace field have a bias stability of 10-50μg, and the Scale factor repeatability is 15-50ppm.
The existing problems and development trend
The advancement of MEMS technology and the improvement of technological level also bring new opportunities to the development of micromechanical accelerometers. By understanding the research dynamics of micromechanical accelerometers at home and abroad, there are several development trends of micromechanical accelerometers in the future:
1. The micromechanical accelerometer with high resolution and large range has become the focus of research. Because the inertial mass block is relatively small, the inertial force used to measure acceleration and angular velocity is correspondingly small, and the sensitivity of the system is relatively low, so it is particularly important to develop a high-sensitivity accelerometer.
2. The development of multi-axis accelerometers has become a new direction. The inertial measurement combination has six output variables, three of which are mutually positive accelerations on the X, Y, and Z axes. There have been literature reports on the development of triaxial micro-silicon accelerometers, and the methods used are different, but its performance is still a long way from practical, and the structural design of multi-axis accelerometers is still a difficult point.
3. small temperature drift, small hysteresis effect has become a new performance target. The accuracy of micromachined accelerometers can be greatly improved by selecting suitable materials, adopting reasonable structure and applying new low-cost temperature compensation link.
If you want to get more details about quartz-accelerometer, pls visit https://www.ericcointernational.com/accelerometer/quartz-accelerometer/
For more information, please feel free to contact info@ericcointernational.com
More Technical Questions
1.Quartz Accelerometer VS MEMS Accelerometer
2.Calibration Method of Accelerometer
3.What is the Quartz Accelerometer Digital Closed Loop Servo Circuit?
4.What are the Advantages and Disadvantages of Quartz Accelerometers?
5.What is Sensitivity and Measurement Range in Quartz Accelerometer?
6.How to Improve the Long-term Stability of the Quartz Accelerometer?
Products in Article
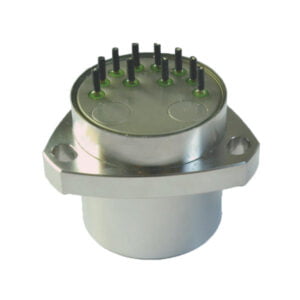
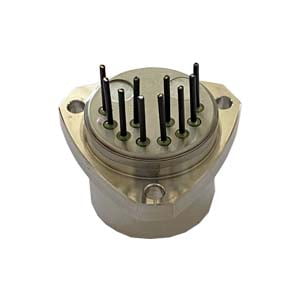
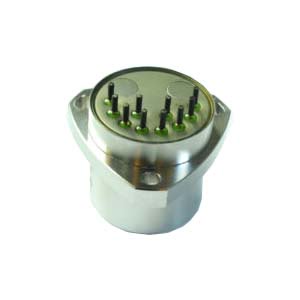
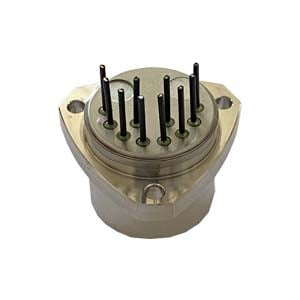
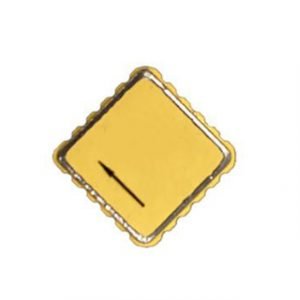
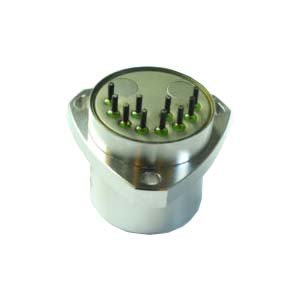