MEMS (Micro-Electro-Mechanical System) refers to a complete micro electromechanical system that integrates mechanical elements, micro sensors, signal processing and control circuits, interface circuits, communication and power supply. MEMS inertial sensor can form a low-cost INS/GPS integrated navigation system. It is a kind of inertial sensor that is very suitable for building a miniature strapdown inertial navigation system. The outstanding characteristics of MEMS inertial sensors make them have broad application prospects in many civil and military fields.
Background condition of MEMS inertial sensor
MEMS technology was first conceived by Richard Pfeynman (who won the Nobel Prize in Physics in 1965) in 1959. In 1962, the silicon micro pressure sensor came out.
In 1979, Roylance and Angell began the development of piezoresistive micro-accelerometers. In 1991, Cole began the development of capacitive micro-accelerometer.
Inertial sensors include accelerometers (or accelerometers) and angular velocity sensors (gyroscopes) as well as their single, dual and three-axis IMU (inertial measurement unit) and AHRS (attitude reference system including magnetic sensors).
MEMS accelerometer is a sensor that uses the inertial force of the sensing mass to measure, and generally consists of a standard mass block (sensing element) and a detection circuit. According to the different sensing principles, there are mainly piezoresistive, capacitive, piezoelectric, tunnel current, resonant, thermoelectric coupling and electromagnetic.
In 1998, CSDL of the United States designed and developed the earliest MEMS gyroscope. In the same year, Drapor laboratory developed another form of MEMS gyroscope. MEMS gyroscope is made by using the Coriolis effect when the vibrating mass is driven by the base (shell) to sense the angular velocity.
The main forms are frame-driven (inner and outer frame) comb-driven, electromagnetic driven, etc.
IMU is a micro inertial measurement unit of MEMS technology combination, so it is called MIMU in many places. It is mainly composed of three MEMS acceleration sensors, three gyroscopes and solution circuits.
AHRS is an IMU with three magnetic sensors, and it can directly output the pitch angle, roll angle and heading angle of a moving body through the calculation based on the four-element method.
As consumer electronics products, high-precision MEMS inertial sensors are mainly used in mobile phones, game consoles, music players, wireless mice, digital cameras, PDs, hard disk protectors, smart toys, pedometers, anti-theft systems, GPS navigation and other portable devices. Because of its basic measurement functions such as acceleration measurement, tilt measurement, vibration measurement and even rotation measurement, consumer electronics applications to be explored will continue to emerge.
Intermediate MEMS inertial sensors, as industrial and automotive products, are mainly used in the electronic stability system (ESP or ESC) of automobiles, GPS aided navigation system, automobile airbags, vehicle attitude measurement, precision agriculture, industrial automation, large medical equipment, robots, instruments, engineering machinery, etc. As military and aerospace grade products, high-precision MEMS inertial sensors mainly require high-precision, full-temperature range, impact resistance and other indexes. It is mainly used for stability applications such as communication satellite wireless, missile seeker, optical aiming system, etc; Aircraft/missile flight control, attitude control, yaw damping and other control applications, as well as medium-range missile guidance, inertial GPS navigation and other guidance applications, long-range aircraft and ship instruments, battlefield robots and so on.
Working principle of MEMS inertial sensor
MEMS inertial sensor is a micro-electromechanical system based on integrated circuit technology and micromachining technology, which is manufactured on a single silicon chip, including micromechanical accelerometer, micromechanical gyroscope and micro inertial measurement unit (MIMU). The working principle of MEMS inertial sensor is Newton's law in classical mechanics. Its function is to measure the centroid motion and attitude motion of moving objects (such as vehicles, aircraft, missiles, ships, satellites, etc.), and then control and navigate the moving objects. Compared with non-MEMS inertial devices, the volume and price of MEMS inertial devices can be reduced by several orders of magnitude, which is of great strategic significance to national defense. The construction of low-cost and high-performance micro inertial navigation system based on MEMS inertial devices is becoming a research hotspot in the field of inertial technology.
Test of MEMS inertial sensor
The difference between the test of MEMS inertial sensor and general IC test is that it requires external stimulation. Therefore, in addition to the common configurations such as automatic test equipment (ATE), ATE interface panel (DIB) and device nest board (DUT board), it also requires an extremely important equipment - equipment for generating and transmitting stimulation. This device is customized. Different sensors, especially different types of sensors, use different or even completely different devices. Therefore, such equipment is often not standardized in industry. Customers must develop corresponding equipment together with equipment manufacturers when designing new inertial sensors. The cost of this development is very expensive, in millions of dollars. Even if the sensor package is changed, the test surface or cavity must be redesigned, which usually costs $200000, 8 to 12 weeks. If there is no agent testing factory, even if small companies can design and produce inertial sensors, it is difficult to sell them in large quantities.
In addition, the test time is an important factor affecting the cost of the product, especially the inertial sensor, because the mechanical stimulation is often much slower than the general circuit measurement. Moreover, mechanical stimulation must wait for enough time to stabilize after triggering, and must wait for enough time to completely disappear after switching off. In order to shorten the test time, in addition to improving the mechanical design of the equipment, improving the test parallelism is an immediate way.
Applications of MEMS sensors
The main application fields of MEMS micro inertial sensors are automobiles, inertial navigation, consumer electronics and IT accessories. The figure below shows the MEMS application in automobiles. It can be seen that accelerometers and gyroscopes account for a large proportion. At present, due to the high price of micro gyroscope, its application potential has not been fully developed, but if there is a breakthrough in technology that greatly reduces the production cost of gyroscope, there will be great market potential in the navigation system.
The main development direction of micro inertial devices in the future is to minimize and reduce the price on the premise of meeting the accuracy and stability of civil demand. In particular, gyroscope, only by reducing the price of gyroscope, the integrated IMU (inertial measurement unit, including three gyroscopes and three accelerometers) can be widely used in virtual reality (motion perception) in automobile navigation and entertainment electronics.
Development trend of MEMS inertial sensors
The development trend of MEMS inertial sensors mainly includes the following aspects:
1.In terms of technology: the accuracy will continue to improve. Take gyroscope as an example, there is a trend to replace the low precision fiber optic gyroscope. For consumer applications, the trend is to further simplify the manufacturing process and reduce costs. At the same time, integration is also the trend of future development. Not only do module manufacturers take the path of software and hardware integration, but more and more upstream chip manufacturers also take the path of integrated block technology. As a result, there are more and more dual-axis, three-axis accelerometer and gyro chips.
2.In terms of competitiveness: the competition for consumer products will be the most fierce, and new manufacturers will continue to pour in. Comparing investment and scale will be an inevitable trend. The competition, acquisition and reorganization between upstream and downstream will be staged.
3.Cooperation: due to product segmentation, global competition and cooperation are inevitable results. Upstream manufacturers want to find downstream customers, and downstream manufacturers want to find suitable suppliers, so industrial alliances may appear.
4.Application: There is no doubt that the market will expand rapidly and the application will become more and more widespread, whether it is consumer application or industrial military application.
More Technical Questions
1.How to Distinguish MEMS Accelerometer and MEMS Gyroscope Correctly?
2.How to Improve the Sensitivity of MEMS Gyroscope?
3.How do MEMS gyroscopes work?
4.MEMS gyroscopes, accelerometers and magnetometers
5.Application of MEMS Accelerometer in North Finder
6.How MEMS ‘accelerate’ North Finder
Products in Article
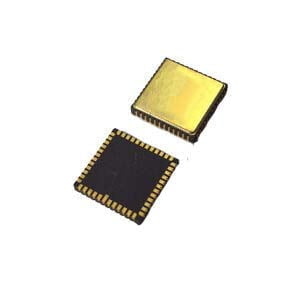
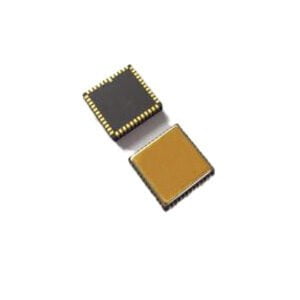
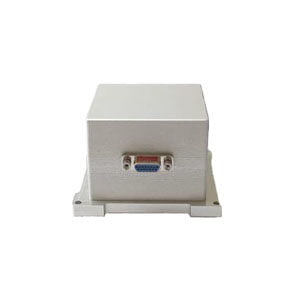
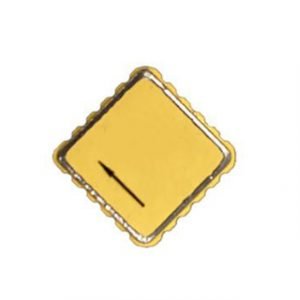
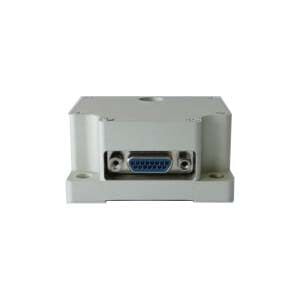
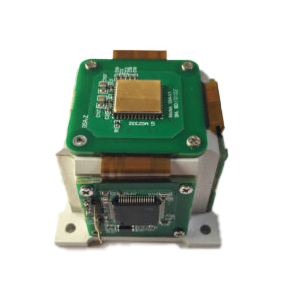