Gyroscope measurement is an essential part of drilling, and the harshest use environment for gyroscopes is the oil and gas downhole drilling industry. In the construction of cluster well groups, due to the influence of magnetic interference between wells, the error of MWD inclination data is large, and the product is also easily affected by the impact and vibration of the drill string. This type of abuse will lead to excessive wear of the system and premature failure, resulting in high maintenance or downtime costs. Compared to equivalent discrete sensors, MEMS are generally smaller and consume less power and cost.With a volume of just 11 x 11 x 2mm, the ER-MG2-50/100 gyroscopes also have a bias instability of 0.01 to 0.02°/hr and an angular random walk of 0.0025 to 0.005°/√hr, capable of measuring angular velocities up to ±100°/s. It also has a digital output that conforms to SPI slave mode 3 protocol. Angular rate data is expressed as 24-bit words. In addition, they can integrate signal conditioning circuits in the same size semiconductor package.
By applying micro-electromechanical (MEMS) technology, the internal vibration structure is used to determine the rotation rate, and then the parameters such as well inclination, azimuth, and tool face are determined, which overcomes the influence of the Coriolis effect and improves the system performance of the gyroscope while drilling. The technology can also be applied to robots, spacecraft, and mobile devices. The MEMS gyro inclinometer can obtain measurement data in real time after the pump is stopped, and it does not need to wait for 30 minutes like a mechanical gyroscope, thus greatly improving the construction efficiency. Compared with mechanical gyroscopes, MEMS gyroscopes are designed to use solid-state sensors, which can withstand extreme conditions such as downhole shock and vibration, do not require recalibration during use, and consume less energy. The same battery can be used for a longer time. The field application of the instrument shows that the MEMS gyro MWD can meet the accuracy requirements required by today's complex drilling environment, and when used in conjunction with the MWD measurement tool, the uncertainty can be reduced by 45%, which is beneficial to the precise control of the trajectory and the target hit.
The MEMS gyroscope uses the internal vibration structure to determine the bit speed, and then determines the well inclination, orientation, tool face and other parameters, so as to realize the real-time monitoring of the well trajectory and the bit position, and ensure that the well depth reaches the predetermined position. Unlike traditional sensors, MEMS gyroscopes have obvious advantages in drilling applications: compared with discrete sensors, MEMS gyroscopes are smaller, lower power consumption and lower cost; MEMS gyro inclinometer can obtain the measurement data in real time after stopping the pump, without waiting 30 minutes like mechanical gyro, which greatly improves the construction efficiency and reduces the construction cost. At the same time, compared to mechanical gyros, MEMS gyros can withstand extreme conditions such as downhole shock and vibration, do not need to be recalibrated during use, and consume less energy.
At the same time, the oil drilling industry also needs sensors that can operate at high temperatures, especially easy-to-use sensors provided by microelectromechanical systems (MEMS). In order to meet this demand, ERICCO has launched a north-seeking MEMS gyroscope ER-MG2-100 which is designed for north finding, pointing, initial alignment/gyroscope tools, mining/drilling equipment, weapons/UAV launch systems, satellite antennas, target tracking systems, etc. Due to its high performance, it can also be used for high-precision attitude measurement, stability control, positioning, navigation-grade MEMS IMU/ INS, land surveying/land mobile mapping systems, railway train systems, and more.
With the oil and gas industry just recovering from a prolonged downturn, there is a strong need from operators to improve downhole well intelligence, improve technical reliability, speed up drilling and reduce the cost of networking downhole operations. Together, these factors ushered in a new era of microelectromechanical systems (MEMS)-based directional drilling sensor technology.
More Technical Questions
2.How do MEMS gyroscopes work?
3.How accurate is MEMS gyroscope?
4.How to select MEMS gyroscope?
5.What Data Format is High Performance MEMS Gyro
6.How to Configure the Register of Ericco MEMS Gyro
Products in Article
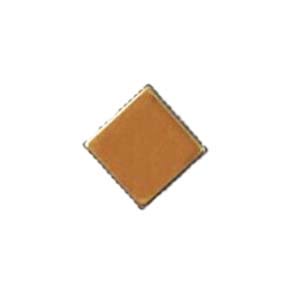
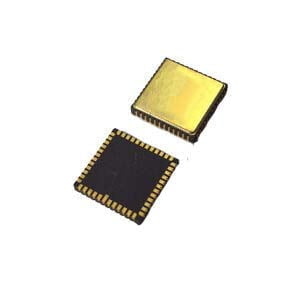
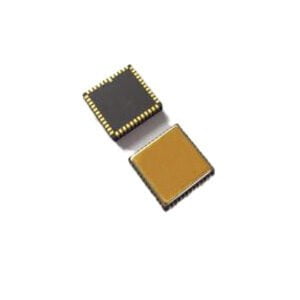
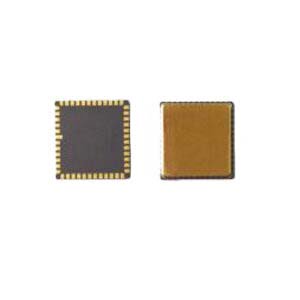
.jpg)
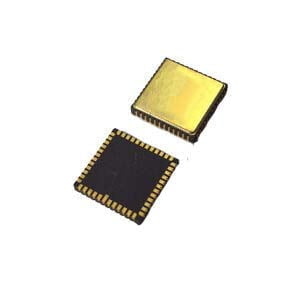