ER-PMINS Pipe Inertial Mapping System
Introduction
ER-PMINS Pipe Inertial Mapping System can measure the trajectory, coordinate of oil and gas pipeline, and do meter grade positioning, assisted pipeline safety assessment and damaged point positioning. With the advantages of a highly automatic, low power consumption, long term working and the centimeter grade measurement precision of pipeline deformation. The product has successfully applied in CNOOC, petro china pipeline detection engineering application.
Features
Long time high precision navigation technology (100h+);
High precision correction technology in mark spot;
Spiral trajectory error compensation technology;
Closed pipe "special situation" processing technology;
Pipeline environmental adaptability technology;
Accurate positioning in pipeline surveying and mapping.
Applications
Pipeline detection
Pipe mapping inertial navigation system
Specifications
Measurement range
Speed range | -50 m/s~50m/s |
Pitch angle | ±90° |
Roll angle | ±180° |
Heading range | 0°~360° |
Measurement Precision
Height | ±2m (1σ) |
Horizontal positioning accuracy (east, north) | ±2m (1σ) |
Pitch angle (initial alignment) | ±0.15 ° |
Roll angle (initial alignment) | ±0.15 ° |
Heading angle (initial alignment) | ±3 ° |
Application Techniques
1.Research Background and Current Status of MEMS IMU
2.Internal Structure Analysis of IMU
3.What are the Application Scenarios of the IMU?
4.MEMS and FOG: How Should you Choose Inertial Navigation System?
5.FOG Inertial Navigation System Comparison Test
6.How does the Quartz Accelerometer Work?
More Products
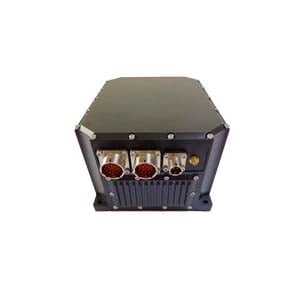
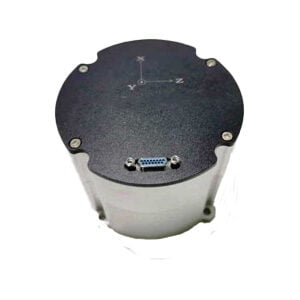

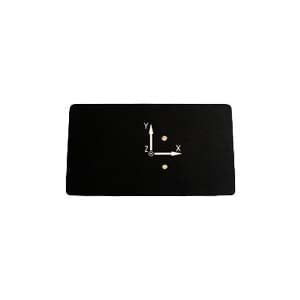
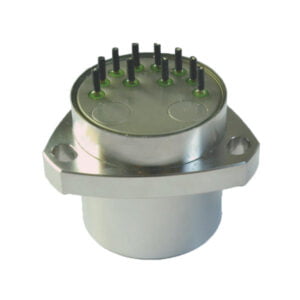
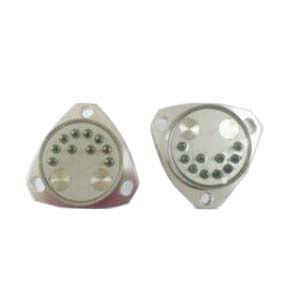