The main substance of MEMS gyroscope is silicon, and its physical properties change with temperature. In addition, the assembly structure and electronic components of MEMS gyroscope are also highly sensitive to temperature changes, which causes the zero bias of MEMS gyros to fluctuate with temperature changes. When the working environment temperature changes, the previously calibrated static zero bias parameters will also shift greatly with the well depth temperature and self-heating.
In recent years, in the exploration and exploitation of oil and gas resources, a large number of high-quality oil and gas resources that are easy to exploit are becoming less and less, and the exploration of oil and gas resources has begun to shift to areas with complex terrain, scattered oil layers and difficult exploitation. In this special exploration and production environment, the traditional vertical drilling technology can not meet the requirements of current oil and gas resource acquisition, whether the drilling with a certain slope and strike can be carried out according to the planned trajectory will directly affect the success of drilling. In recent years, directional borehole trajectory exploration, small-diameter borehole trajectory exploration and horizontal borehole trajectory exploration have been gradually developed, which have the characteristics of low cost, small volume and high production efficiency, and have gradually become the mainstream drilling technology in major oil and gas fields at home and abroad. The key of directional drilling technology in the process of exploration is the acquisition of borehole trajectory. Whether the drill bit can drill accurately according to the planned trajectory determines whether the petroleum exploration system can reach the designated oil layer for oil exploitation.
Due to the continuous progress of MEMS technology, MEMS gyro is gradually used as a part in key instruments and equipment. This paper introduces three methods to compensate the zero bias drift of MEMS gyro.
Method of compensating MEMS gyroscope zero bias drift
In order to reduce the influence of temperature change on the measurement accuracy of MEMS gyro and improve the measurement performance of MEMS gyro, it is necessary to correct and compensate the gyro zero deviation caused by temperature change in real time. At present, there are three main methods to reduce the zero-bias drift of MEMS gyro:
1. The first method is to start from the design of the device itself, develop a MEMS gyroscope with higher precision, optimize its internal sensor structure design, and reduce the dependence on temperature. This method can fundamentally improve the overall performance of MEMS gyro, but it will make the processing technology become complicated, the technical difficulty of sensor design increases, and the cost increases.
2. The second method is to study the relationship between MEMS gyro temperature and output signal at each static temperature point. The zero deviation experiment of each temperature point was carried out before drilling, and the temperature compensation model was established. The working temperature was obtained by the temperature sensor during the operation of the inclinometer, and the static temperature compensation model was directly used to compensate the actual drilling dynamic temperature. This method is simple in structure and easy to implement, but it does not consider the zero-bias drift in the dynamic temperature change environment, and the adaptability of the zero-bias compensation model is poor.
3. The third method is to add temperature control equipment to the inclinometer system and adopt strict insulation devices to control the temperature of the inclinometer without great changes. This method not only increases the overall volume of the clinometer system, but also for offshore ultra-deep well oil exploration, the temperature range covers from -20℃ of the derrick platform, with the oil well drilling can reach 125℃, even 150℃, and the survey working time is generally more than 12h, the method of adding insulation device to the system is not suitable for long-term application environment at sea.
Aiming at the operating environment of dynamic temperature variation, this paper proposes a dynamic temperature variation compensation scheme. By carrying out dynamic temperature variation experiment in a high and low temperature chamber, the real-time output data of gyroscope is obtained to carry out temperature compensation. Because the output of MEMS gyroscope contains a lot of noise interference, which is not conducive to the fitting of dynamic temperature curve, it is necessary to de-noise the original measurement signal of the gyroscope first. In this study, the wavelet multi-scale filter, which is more mature in laboratory application, is used to denoise the noise, and then the output function is fitted to the filtered data, and the zero bias compensation is carried out in real-time dynamic temperature change environment.
Conclusion
This paper introduces three methods to compensate the zero bias drift of MEMS gyro. MEMS gyroscope is a very popular choice in all walks of life, its accuracy level is very important, and it is very important to use various effective methods to compensate the error. Ericco mainly develops MEMS gyroscopes, which are fully compensated at the time of appearance and are strictly calibrated. ER-MG2-50/100 is a north seeking MEMS gyroscope, it is a navigation-grade gyroscope, its zero bias instability can reach 0.01-0.02°/hr, angular velocity random walk can reach 0.0025-0.005°/√hr. Likewise, Ericco has a number of tactical grade and two - and three-axis MEMS gyros.
If you are interested in learning more about MEMS gyroscope, please contact us.
More Technical Questions
1.Integrated method of three-axis MEMS gyroscope
2.Development history of MEMS gyroscope
3.MEMS gyroscope processing technology
4.Research on driving mode of MEMS gyroscope
5.Stochastic error modeling method of MEMS gyroscope
6.Signal Denoising Principle And Evaluation Index of MEMS Gyroscope
Products in Article
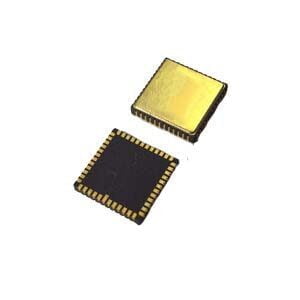
High precison MEMS Gyroscope
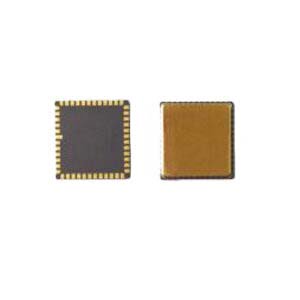
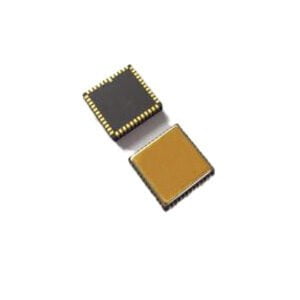
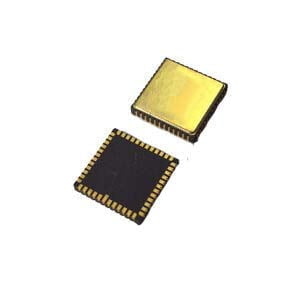
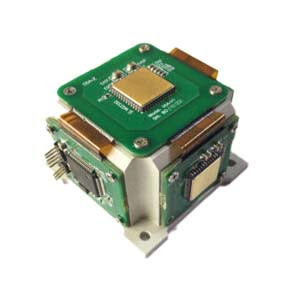
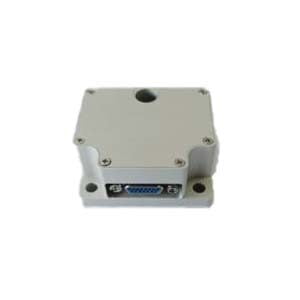
High Precision Stable-Control MEMS IMU