North finders are widely used in military and civilian fields, and are not affected by terrain, climate, external magnetic fields, measurement time, measurement points, and measurement conditions, and can independently find true north with high accuracy. The main advantage of a gyroscopic north-seeker alignment instrument over a magnetic compass is that a gyroscopic north-seeker points to true north rather than magnetic north, and is not affected by the surrounding ambient magnetic field.
MEMS north finders have great application prospects in the field of inertial north-seeking. Compared with traditional gyro north-seeking direction alignment instruments, MEMS north-seeking direction alignment instruments has obvious cost advantages. In addition, size, weight and power are also highlights, which can shorten the gap between low-cost alignment instruments and small, low-weight, low-power portable devices.
1.Definition of full temperature compensation
Simply put, temperature compensation refers to the method of eliminating errors caused by changes in temperature during the measurement process by compensating for temperature. In many fields, such as industrial automation, aerospace, medical equipment, mining and drilling, etc., So temperature compensation is very important.
2.Why does temperature affect the north finder?
The MEMS gyroscope built into the north seeker is a temperature-sensitive device, and its material is semiconductor silicon. When the temperature changes, the thermal expansion coefficient, elastic modulus, resonant frequency, etc. of the silicon wafer will change.
The two most important performance indicators of north finder, one is the scale factor, the other is zero bias, zero bias and scale factor will be affected by the temperature characteristics, and the zero bias value is affected by the size of the factor, so the size of the scale factor affects the performance of the north finder equipment, therefore, we must pay attention to the scale factor. During downhole operation, the performance of MEMS north finder is affected by complex ambient temperature changes. The temperature will affect the head size structure of the gyroscope, the performance of the components, the elastic modulus of the material and the resonance frequency, so as to affect the zero bias and scale factor of the internal core sensor MEMS gyroscope. Because the components of the gyroscope and the performance of electronic components are very sensitive to temperature changes, the measurement accuracy of the MEMS gyroscope will be seriously restricted. As the core component, gyro will have an important influence on the accuracy of the north-seeking alignment instrument.
3.The benefits of the north finder after full temperature compensation
MEMS series of north seeking alignment instruments integrate cost-effective MEMS gyro and accelerometer in an independent structure, and carry out zero position of all temperature parameters, scale factor, non-orthogonal error and compensation of acceleration-related terms within the system, which can maintain a high measurement accuracy for a long time.
Total temperature compensation is a correction process to eliminate the error of the north seeking alignment instrument under different temperature conditions. At different temperatures, the characteristics of the core components of the north finding equipment may change, which will affect the accuracy of the measurement results. After the full temperature compensation, the influence of temperature on the north finding equipment can be corrected. Improve its accuracy and reliability.
4.Temperature experiment and temperature characteristic analysis
The influence of temperature on gyro is manifold. It is difficult to summarize the temperature drift model by physical formula. It is a feasible measure to use system identification method to determine the model structure and parameters. Firstly, the temperature and gyro output data are obtained through temperature experiment, and then the temperature compensation model based on polynomial fitting is determined, and the coefficient of the model is estimated by the least square method.
Three temperature ranges of 0℃ ~ 20℃, -40℃ ~ -20℃ and 40℃ ~ 60℃ were selected for the temperature test, the temperature box was set as the initial value, and the gyroscope was kept in the temperature box for 4h. When the temperature of the gyroscope was the same as the temperature of the temperature box, the gyroscope was started and the temperature box was raised and cooled at a change rate of 5℃ / h, and the temperature and output data of the gyroscope were recorded.
Figure 1 shows the connection diagram of the test equipment. The temperature box error used in the test is ±0.5℃. The gyro output data in X, Y and Z directions are recorded in the test. The three axes are independent of each other and there is no connection between their outputs. The gyro output data usually contains a lot of high-frequency noise. In order to identify the trend of gyro output with temperature more easily, 10s are smoothed when analyzing gyro output data.
Summary
In the MEMS technology series independently developed by Ericco, direction alignment instruments ER-MNS-05 has a quite mature full temperature compensation function, which is very suitable for mining, drilling and other construction environment harsh engineering projects. Not only can reduce the north error, anti-interference, but also suitable for small detection space of the project. In addition, Ericco has the world's smallest MEMS north finder ER-MNS-06, small in size, but fully functional, if you are interested, you can view the specific product information.
More Technical Questions
1.Application of Wavelet Domain Median Filter in North Seeker
2.Technical analysis of MEMS direction alignment instrument for mining
3.Research on downhole north seeker
4.Research on orthogonal monitoring technology of north finder
5.Modeling and filtering in signals collected by FOG north seekers
6.Error Modeling and Compensation Analysis of North Finder Based on FFT
Products in Article
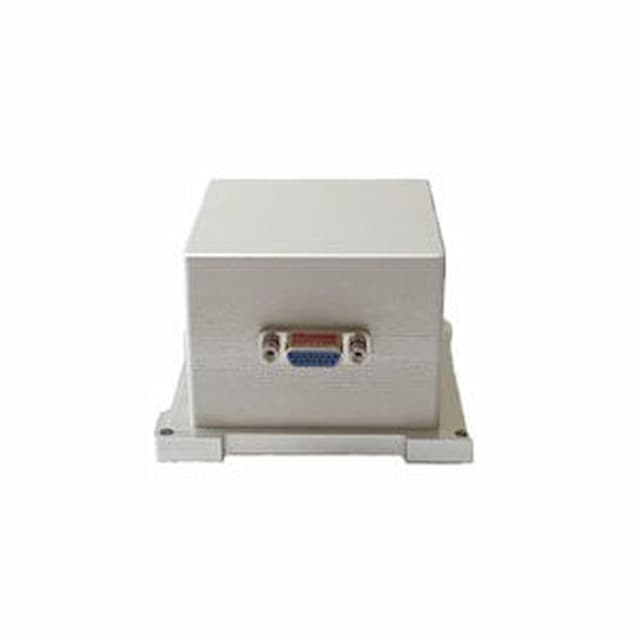
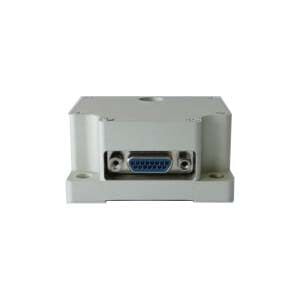
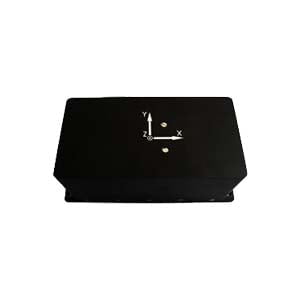
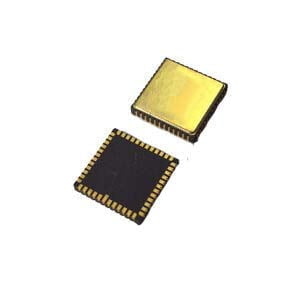
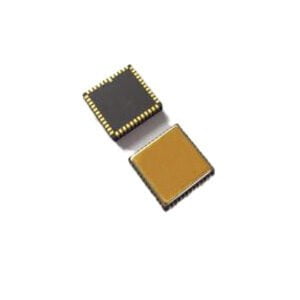
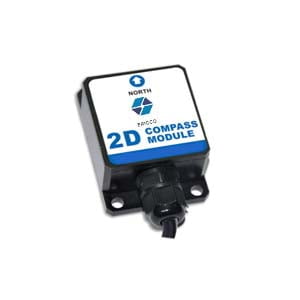