Background
The north finder based on MEMS technology is an important part of the borehole orientation instrument scheme, which provides the azimuth reference for the whole scheme, and its north finding accuracy determines the overall accuracy of the scheme. The inertial measurement and inertial positioning system developed on the basis of inertial navigation system can be used in geodetic survey, map drawing, pipeline laying, oil drilling positioning, robot control and other large-scale measurement and accurate positioning.
With the development of electronic technology, measurement and control technology and computer technology, the safety guarantee system of underground mining has been continuously combined with the above technical fields, among which, underground physical exploration of coal mine is an important work before mining, namely: In the place where the gas may be predicted in advance, the gas should be extracted from the gas layer in advance under the guidance of accurate positioning to avoid safety accidents in the process of mining and excavation.
In the process of north seeking, the north finder is mainly affected by the gyro measurement error, the influence of the Angle of position, these errors are directly related to the performance of the finished product and the use of the end user, so it needs to be combined with a certain theory and engineering means to solve, the following analysis, put forward the implementation of the project engineering solutions.
MEMS technical support
The performance and measuring point latitude of MEMS gyro affect several performance system characteristics of gyro, and will affect the north finding accuracy. However, the problem of performance can be selected through the screening of indicators to select a more suitable gyroscope. The following is mainly discussed: the error term caused by the different physical input conditions, after calculation, can be corrected by the algorithm to reduce the impact of the error. The ideal output of a MEMS gyroscope during north finding is:
In this formula, ωe is the earth's rotation speed, L is the geographical latitude of the measurement location, ϕ is the Angle between the MEMS gyro's sensitive axis and true north, and ω is the angular velocity of the MEMS gyro's measurement output.
For north seeking, MEMS gyroscope differentiates azimuth difference by sensitive to the velocity component of the Earth's rotation. Differentiating ϕ over the above condition gives the following equation:
It can be seen from the formula that the performance of the north seeking error caused by the measurement error of the gyroscope is different at different north seeking positions. When the direction of the sensitive axis is 0° or 180°, the Angle of the gyroscope output will be affected. At 90° or 270°, it is relatively stable. Therefore, the pre-estimation of azimuth is helpful to improve the north seeking accuracy to some extent. This scheme can effectively improve the north seeking accuracy by using the quadratic north seeking method of predicting Angle and measuring Angle. In addition, combined with certain calibration and compensation measures, the prototype can give the north finding accuracy close to the theoretical level, which undoubtedly increases the design redundancy and improves the yield of the delivered products.
Summary
Ericco introduced a mining MEMS three-axis north finder ER-MNS-09, which has a self-alignment function, and then adds attitude tracking function on this basis, and is also the first shaped north finder, which can be placed in the probe, suitable for engineering projects with special requirements for monitoring the environment. In addition, we also offer the cost-effective three-axis north finder ER-MNS-05 and the world's smallest MEMS three-axis north finder ER-MNS-06, if you are interested, welcome to explore together.
More Technical Questions
1.Effective combination of north finder and spacecraft based on autonomous orientation
2.Research on downhole north seeker
3.Research on orthogonal monitoring technology of north finder
4.Modeling and filtering in signals collected by FOG north seekers
5.Error Modeling and Compensation Analysis of North Finder Based on FFT
6.Research and use of north finder for mining drilling rigs
Products in Article
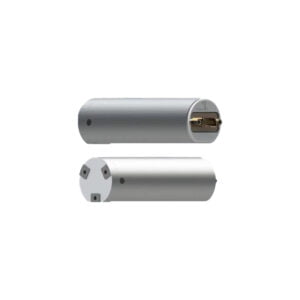
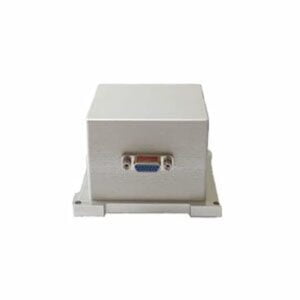
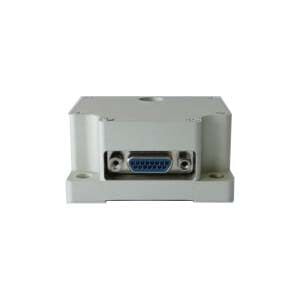
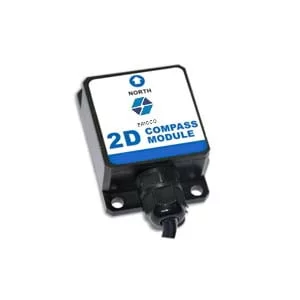
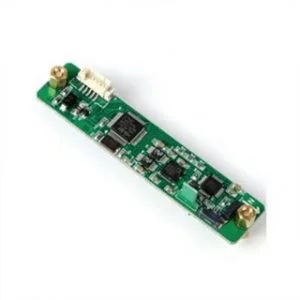
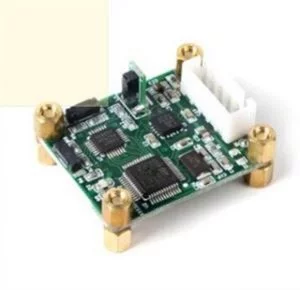