With the development of science and technology and various measurement techniques, the emergence of gyro theodolite has changed the traditional geometric orientation method and has been widely used in various measurements in mines. Orientation accuracy is an important indicator for evaluating the quality of gyro-theodolite, but during the measurement process, many factors will affect its measurement accuracy. Normally, the orientation accuracy error of a gyro-theodolite is controlled within the nominal range when leaving the factory. However, due to limitations of the manufacturing process level, the use of the instrument, and the influence of external conditions, the orientation accuracy may be reduced, which meets the requirements. The actual requirements for measurement cannot be met. Therefore, the analysis and research on the orientation accuracy of gyro-theodolite has important theoretical value and practical significance.
1.Composition and measurement principle of gyro-theodolite
Gyro theodolite is a theodolite with a gyroscope device used to measure the true azimuth angle of a straight line. It is mainly used in mine construction measurements, tunnel construction measurements, and horizontal and true north direction measurements in shield tunneling. It is not affected by time and environment. Observation is simple, convenient and efficient. A suspended gyroscope is installed on the theodolite. Its key device is a gyroscope, referred to as a gyroscope. It is mainly composed of a rigid rotor that rotates at high speed around the gyroscope axis and is supported on one or two frames. Currently, three precision orientation methods of gyro-theodolite are commonly used: tracking reversal point method, midheaven method and gyro rest position method. The principle of orientation is mainly to use its north pointing property to determine the north direction of the true meridian, and then use the theodolite to measure the horizontal angle between the north direction of the true meridian and the direction to be determined, that is, the true azimuth angle. The rotor is usually driven by a gyromotor, causing it to rotate around the gyro axis at high speeds, with speeds as high as several thousand to tens of thousands of revolutions per minute. The orientation method is determined by the two basic characteristics of the gyro itself: fixed axis and precession. The fixed-axis nature of a gyroscope means that when a gyroscope rotating at a constant speed is not affected by any external force, that is, when the external torque is zero, it strives to maintain its own rotational inertia so that its rotation axis points to the constant initial direction of the inertial space. characteristics, that is, stability; the precession of the gyro means that when the gyro is acted upon by an external torque, the rotation axis of the gyro moves in the direction of the external torque.
2 .Factors affecting measurement accuracy
The measurement accuracy of a gyro-theodolite refers to the degree of deviation between the directional observation value of the gyro-theodolite and the true value. There are usually many factors that directly affect the measurement accuracy of a gyro-theodolite.
(1) Environmental factors.
Some gyro-theodolite have high environmental requirements, and there are many environmental factors that affect the measurement accuracy. Among them, temperature has the greatest impact. Some instrument manufacturers perform temperature compensation processing on the measurement results inside the instrument, but the impact of temperature on the measurement results is It is multi-faceted and very complex. This effect cannot be well eliminated by relying only on the temperature compensation adopted by the manufacturer.
(2) Factors when connecting theodolite and gyroscope.
The theodolite and the gyroscope are connected through a transition bracket fixed on the collimation part. The gyroscope needs to be placed on the theodolite bracket every time it is oriented. Therefore, each disassembly and installation may affect the measurement results. Accuracy.
(3) Factors affecting changes in swing equilibrium position.
Changes in the frequency of the power supply voltage will cause changes in the angular momentum, or changes in the internal temperature of the sensitive parts will also cause the center of gravity to shift and the temperature to rise, causing the suspension belt and the guide wire to deform, causing an interference torque to act on the sensitive parts. , causing the balance position to change, and the change in the balance position is uncertain, resulting in a reduction in the measurement accuracy of the gyro-theodolite.
(4) Drift factors of gyro-theodolite.
The drift of gyro-theodolite is mainly divided into long-term and short-term. The long-term drift period is generally several months and years, and the long-term drift period of each instrument is generally different. In actual use, the influencing factors of short-term drift are more obvious. In chronological order, short-term drift can be divided into three-level, two-level and primary drift. Therefore, when in use, the gyroscope should be brought into a more regular second-level drift period as soon as possible in order to achieve accurate orientation.
(5) Gyro-theodolite centering and leveling factors.
When the bubble of the instrument is not centered in the east-west direction, it will cause deviation in the suspension belt part of the gyroscope, causing orientation errors and affecting orientation accuracy.
3. Suggestions for improving measurement accuracy
Considering various factors that affect measurement accuracy and combined with practical engineering experience, the following suggestions are put forward to improve measurement accuracy.
(1) When measuring orientation, the instrument must be used by a person with certain operating experience, and the constants of the instrument must be measured several times, which should generally be completed within three days and nights.
(2) In relatively harsh external environments, such as strong wind, heavy rain, heavy fog and other weather conditions that are not suitable for gyro orientation, a forced centering device should be used for centering to eliminate the impact of temperature differences on instrument constants as much as possible. Make the instrument temperature consistent with the external environment before performing orientation work. You can also try to establish a temperature compensation model based on the measurement experience and conditions of the instrument used to reduce the impact of temperature on measurement accuracy.
(3) Before starting the gyro motor to reach the rated speed and during the process of braking the gyro motor, the sensitive part of the gyro must be in a locked state to prevent the suspension belt and guide wire from being damaged.
(4) During use, high-precision indoor known edges can be established to analyze the changing rules and stability of the gyro-theodolite instrument constants. The target can be a fixed target with a small aiming error, or a parallel light tube can be used as the target. , when measuring indoors, good environmental conditions must be maintained, such as suitable temperature and stable voltage.
(5) When the sensitive part of the gyro is in a locked state and the motor is rotating at high speed, it is strictly prohibited to move or rotate the instrument horizontally.
(6) For a certain instrument, the measurement results can be continuously observed over a long period of time to analyze and determine the long-term orientation stability and systematic drift patterns of the instrument. In this way, the instrument drift curve with time is established. Based on the curve, selecting the best observation period for measurement will help improve the orientation accuracy.
(6) The gyro-theodolite power supply should be fully charged before operation to prevent the gradual attenuation of the voltage from causing abnormal gyro orientation data and ensure orientation accuracy.
Summarize
Gyro theodolite has the advantages of high measurement accuracy, easy observation, high orientation accuracy, and is not limited by time and environment. It can orient multiple levels underground and other advantages. It is widely used in mining engineering, tunnel measurement, subway engineering and other construction projects. As far as mines are concerned, it completely replaces the long-standing geometric orientation method for domestic mine surveying, and overcomes the shortcomings of the geometric orientation method, which requires occupying the wellbore, causing production shutdowns, consuming a lot of manpower, material resources and time. For example, Ericco's ER-GT-02 can be used in mine measurement and has the following characteristics:
1.Orienteering accuracy ≤3.6" (1σ);
2.Pit interference ability is strong, integrated fuselage design, compact structure, stable performance;
3.Has the functions of low lock, automatic zero observation and etc.
If you want to learn about or purchase a gyro-theodolite, please contact us.
More Technical Questions
1.Application of gyro-theodolite orientation in shaft contact measurement
2.Accurate Alignment Method for Gyro Theodolite Calibration System
3.Application of Gyro-Theodolite Orientation in Mine Surveying
4.Effect of latitude on gyroscopic theodolite
5.What is the Structure of a Gyro Theodolite?
6.How To Orient The Gyro Theodolite?
Products in Article
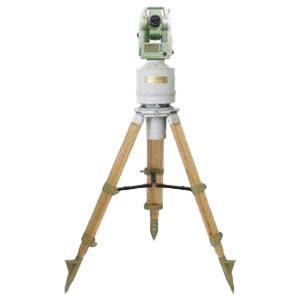
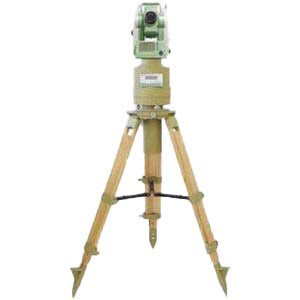
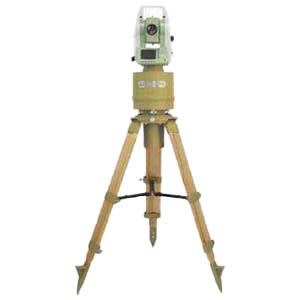
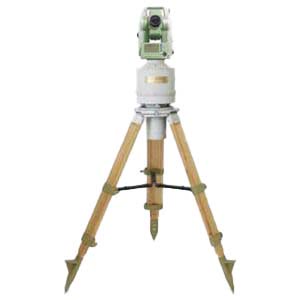

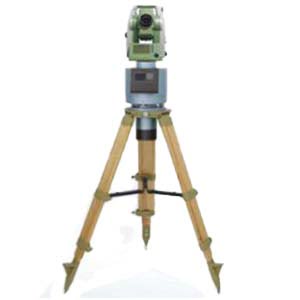