MEMS gyroscope is the third generation gyro in the history of gyro development. It has the advantages of small size, light weight, low cost and easy integration. MEMS gyro driving circuit is one of the components of MEMS gyro interface circuit, which is mainly used to drive the mass block of MEMS gyro to carry out harmonic vibration. Since the performance of the drive circuit directly affects the transient and steady-state characteristics of the simple harmonic vibration of the MEMS gyro mass block, such as the establishment time of the simple harmonic vibration, the overshoot of the establishment process, the amplitude stability of the simple harmonic vibration, the following performance of the vibration frequency relative to the natural frequency of the drive mode and other factors, these factors in turn determine the quality and working reliability of the start-up process of the entire micromechanical gyro system. The linearity and sensitivity of the angular rate are measured. Therefore, the design of the driving circuit of the micromachined gyroscope is very important for the angular rate detection with the micromachined gyroscope.
In this paper, the driving of MEMS gyroscope will be introduced in detail in two ways: open-loop driving and closed-loop driving.
Introduction
MEMS gyros are manufactured using the same silicon wafer processing technology as modern integrated circuits and can be well integrated with interface circuits on a single chip. A common high-precision, low-power MEMS gyro is a differential capacitive structure, as shown in Figure 1. The direction is the driving direction of the MEMS gyros, in which the mass block is driven by AC voltage with DC bias (i.e. driving voltage), and the direction is the detection direction of the MEMS gyroscope. The mass block will also generate vibration in the detection direction due to the Coriolis force. The input angular rate can be determined by detecting the change of differential capacitance caused by vibration in this direction.
MEMS gyro drive circuit is the circuit that generates the above-mentioned drive voltage. According to the way of generating the drive voltage, the drive circuit is divided into two types: open-loop drive circuit and closed-loop drive circuit. The open-loop drive circuit generates the AC part of the drive voltage through the waveform generator. The closed-loop drive circuit directly amplifies the signal equal to the natural frequency of the gyroscope drive mode in the environmental noise through the automatic gain controller, which is used as the AC part of the drive voltage, and the vibration amplitude of the drive mass continues to expand until the system enters a stable working state. The closed-loop drive circuit does not need the AC part of the drive voltage provided by the outside world, also known as the self-excited drive.
As shown in Figure 1, the driving direction of MEMS gyroscope includes two groups of electrodes: the first group is the driving electrode, which is used to apply the driving voltage to provide electrostatic driving force for the mass block; The second group is the drive direction sensitive electrode, which is used to detect the vibration speed of MEMS gyro in the drive direction, and provides the drive circuit to realize the closed-loop drive.
The sensitivity of MEMS gyro is related to the vibration amplitude of mass block in the driving direction. In order to obtain higher sensitivity, it is necessary to make the vibration amplitude of mass block in the driving direction as large as possible, and the vibration amplitude of mass block depends on the DC bias and frequency of the driving voltage. When the frequency of the driving voltage is equal to the natural frequency of the MEMS gyro driving mode, the stable vibration amplitude of the mass block is the largest. Therefore, no matter the open-loop drive or closed-loop drive is used, the mass block is resonant at the natural frequency of the MEMS gyro drive module as much as possible to improve the sensitivity of the system.
Figure 1 Differential capacitive silicon micromachined gyroscope structure
Open-loop drive
The open-loop drive requires the measurement of the natural frequency of the MEMS gyro drive mode in advance in the experiment, and then the AC signal equal to the natural frequency is generated through the waveform generator. As can be seen from Figure 1, the driving electrode has two pairs of electrodes, so it is necessary to generate another AC signal with the same frequency and a phase difference of 180° through the inverting circuit based on the AC signal. The two AC signals are respectively superimposed with a specified DC bias voltage to form a final drive voltage applied to the two pairs of drive electrodes in Figure 1. The principle of MEMS gyroscope open-loop drive is shown in Figure 2.
Figure 2 The principle of open-loop driving method
Usually, the natural frequency of the driving mode of MEMS gyroscope is between several hundred Hz and several thousand Hz, and the AC signal of the driving voltage often chooses to use sine signals. The circuits that can generate sine signals in the frequency range have LC oscillators, RC vibrators and crystal oscillators, etc., because the inductance realization in conventional integrated circuits is difficult, and the RC oscillator circuit is relatively simple. Therefore, the RC oscillator is generally used as the AC signal generator in Figure 2.
The structure of the open-loop drive circuit is relatively simple, and it does not need to detect the vibration amplitude of the mass block in the drive direction and form a closed-loop control. However, this drive mode requires that the natural frequency of the gyroscope drive mode needs to be known before the circuit design. Although the theoretical value of the natural frequency can be determined according to the theoretical value of the MEMS gyro structure design. However, due to the deviation between the actual structure and the theoretical value of the structure design, it is necessary to carry out some measurement work to determine the actual natural frequency of the gyroscope by using open loop drive. In addition, because the natural frequencies of the driving modes of micromechanical gyroscopes in practice will change with the changes of ambient temperature, pressure and other factors, and the difference randomness of the individual natural frequencies of gyroscopes is also relatively large, the practicability of the open-loop driving circuit is relatively poor.
Closed loop drive
In order to achieve closed-loop control of the driving voltage, MEMS gyro not only has a set of driving electrodes, but also needs to set a set of driving direction sensitive electrodes, as shown in Figure 1. When DC voltage is applied to the sensitive electrode in the driving direction, a sensitive current will be generated when the mass block has a displacement change in the driving direction. The frequency of the sensitive current is equal to the vibration frequency of the mass block, the amplitude is determined by the vibration amplitude of the mass block, and the phase difference with the vibration of the mass block is determined by the difference between the vibration frequency and the natural frequency of the driving mode.
When the vibration frequency is equal to the natural frequency, the phase difference is zero, so the closed-loop drive circuit usually only needs to amplify the amplitude without phase shift processing, and with the gradual increase of the drive voltage amplitude, the amplification gain will gradually decrease until the vibration amplitude of the mass block reaches the expected value and enters a stable state, that is, the vibration amplitude is controlled through the variable gain amplifier. The principle of closed-loop drive is shown in Figure 3.
Figure 3 Principle of closed-loop drive method
The closed-loop drive circuit is equivalent to a narrow bandpass filter, the signal whose frequency is equal to the natural frequency of the gyro drive mode in the environmental noise can pass through this filter, and the signals of the remaining frequencies are greatly attenuated, so the drive voltage frequency generated by this drive circuit can follow the natural frequency of the gyro drive mode caused by temperature and other reasons. Because the signal of other frequencies cannot be completely attenuated, there is a certain deviation between the driving voltage frequency and the natural frequency of the gyroscope driving mode, and the frequency jitter is also large. In addition, the circuit extracts useful signals from the environmental noise, and the signals need to be repeated several times in the system composed of the circuit and the gyro structure to achieve stability, so the establishment time is longer. In order to overcome the above shortcomings, PLL (PhaseLockLoop) circuit can be added to the closed-loop circuit to form a self-excited drive circuit based on the phase-locked loop.
Conclusion
This paper studies the principle of open-loop drive and closed-loop drive of MEMS gyroscopes, and analyzes the measures that can be taken in designing the drive circuit of micromachined gyroscope to improve the sensitivity, linearity, build up time and other characteristics of MEMS gyroscope. Among them, the closed-loop drive mode based on phase-locked loop can realize closed-loop control of vibration amplitude. It also has good frequency tracking characteristics and establishment time advantages, which is a good measure to ensure the measurement quality of the whole MEMS gyro system.
For example, the high performance north finding MEMS gyroscope ER-MG2-50/100, with zero bias instability of 0.01 to 0.02°/hr, can be used in north finding, pointing, initial alignment and design/gyroscope tools, mining/drilling equipment, weapons/UAV launch systems, satellite antennas, target tracking systems, etc.
If you want to learn more about MEMS gyroscopes, please click on the related articles and products below.
More Technical Questions
1.Sensitive structure analysis of MEMS gyroscope
2.Bias Temperature Compensation Analysis of MEMS Gyroscope
3.Basic dynamics analysis of MEMS gyroscope
4.Analysis of drive loop noise of MEMS gyroscope
5.Research on scale factor nonlinearity of MEMS gyroscope
6.Packaging of MEMS gyroscope: Structural Analysis of Deep Hole Packaging
Products in Article
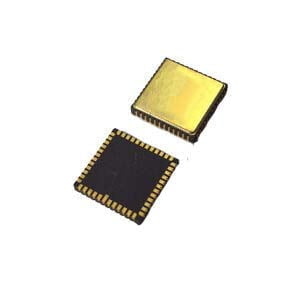
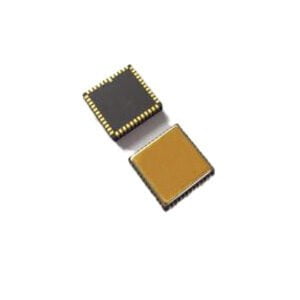
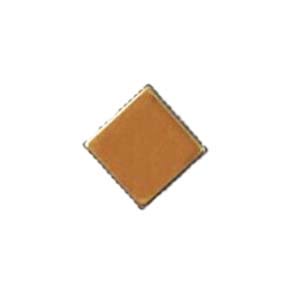
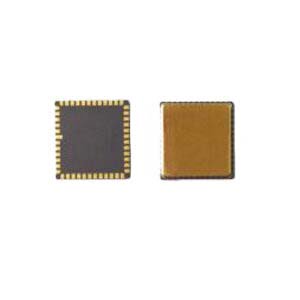
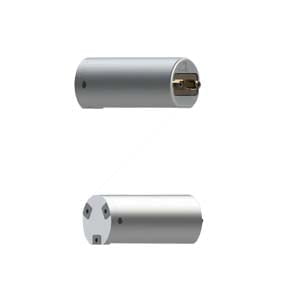
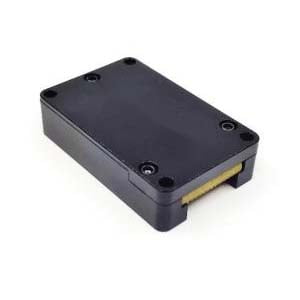