This article delves into the pivotal role of quartz accelerometers in augmenting precision and reliability within petroleum logging operations, elucidating their significance in ensuring accurate and insightful data acquisition.
- Basic Introduction of Quartz Accelerometer:
As vital primary energy sources crucial for human society's survival and development, petroleum and natural gas are anticipated to maintain their dominant energy status until at least 2050. In the constantly evolving oil and gas industry, precision is imperative for informed decision-making across exploration, well construction, and reservoir management endeavors. Quartz accelerometers have emerged as indispensable tools in this realm, providing unparalleled sensitivity and accuracy in capturing crucial data essential for comprehending subsurface conditions.
What is quartz accelerometer?
Quartz accelerometers are crucial components within the measurement while drilling (MWD) process employed by oil and gas companies to establish boreholes for hydrocarbon exploration and production. These sensors, alongside either gyroscopes or magnetometers, collect data to monitor the inclination and azimuth of the drilling hole in real-time. This information empowers the drilling team to navigate the well accurately towards the desired target zone.
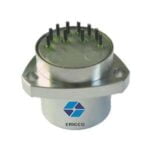
Fig.1 High Performance Quartz Accelerometer
How does quartz accelerometer work?
The quartz flexible accelerometer is a type of force-balanced accelerometer, consisting of a sensor head and a servo circuit, as shown in Figure 2. The flexible pendulum and torque coil form the mass block sensitive to acceleration. When there is an acceleration input, the flexible pendulum deviates from its balanced position. At this point, the dynamic pole plate, which is integral with the flexible pendulum, also moves accordingly from its original position. This deviation is detected by the differential capacitance sensor and converted into an electrical current signal output. Subsequently, it is fed back to the torque generator section, which is in a constant magnetic field, generating a balancing force that compels the flexible pendulum to deviate towards its original balanced position. The magnitude of the current is directly proportional to the magnitude of the acceleration. By measuring the current, the acceleration magnitude can be determined.
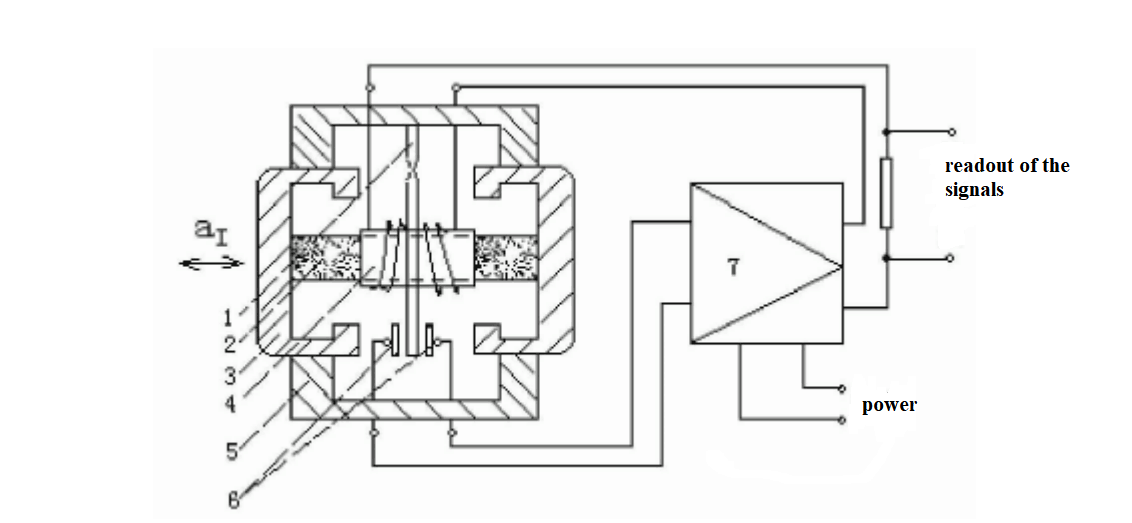
2. Enhancing Depth and Positioning Accuracy:
One of the primary contributions of quartz accelerometers in petroleum logging is their role in improving depth and positioning accuracy. In the petroleum logging industry, it is necessary to measure the actual trajectory of the wellbore and the position of the drill bit to ensure that the well reaches the predetermined location. The accuracy of inclination and azimuth measurements is highly demanded in petroleum exploration. Against the backdrop of increasingly depleted petroleum resources, both domestic and international drilling industries are turning their attention to the exploration and development of complex environments such as offshore, lakes, heavy oil reservoirs, and oceans.
Fig.3 shows the newly developed intelligent drilling navigation system in China.
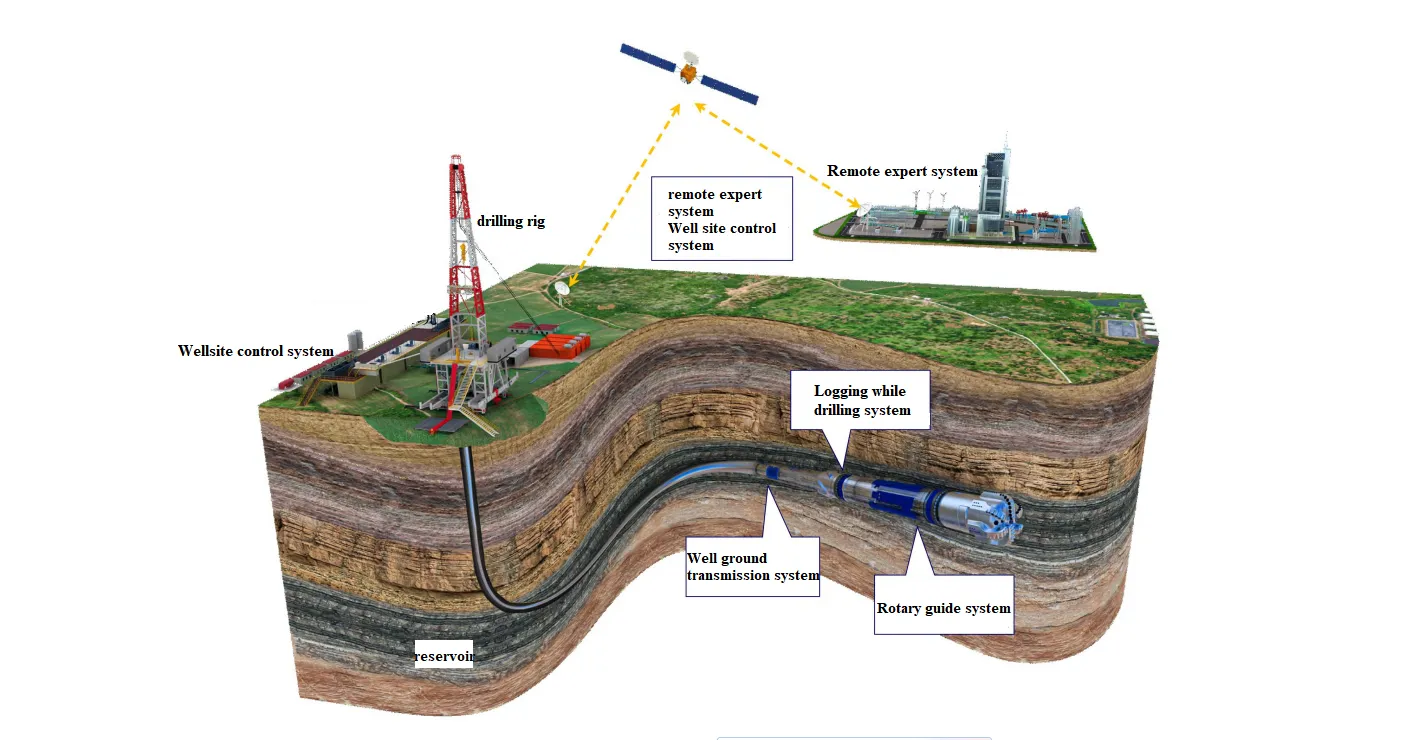
With the increasing number of extended reach wells, high-angle wells, cluster wells, and horizontal wells, there is a growing need for petroleum inclinometers with higher precision and more reliable performance. The application of inertial technology enables this requirement to be met. Inertial-based petroleum quartz accelerometer ER-QA-03D, as advanced measuring instruments widely used in international drilling, can reliably measure acceleration magnitude in high-temperature environments of up to 180°C, which also boasted high accuracy, with bias repeatability <50μg, and scale factor repeatability <80 ppm. Together with results of other sensors, the data tested in deep wells is accurately and timely fed back to the surface control center, achieving precise navigation of drilling direction through remote control systems.
3. High temperature and high pressure technology research of quartz accelerometer
In deep/ultra-deep drilling operations, the acquisition of core information and data such as directional positioning, drilling condition monitoring, heavily relies on high-temperature, high-pressure, high-sensitivity sensors. However, achieving precision and environmental adaptability of sensors in high-temperature and high-vibration environments involves a blend of mechanical, materials science, microelectronics, and control science, posing a frontier technological challenge in the sensor field. Focusing on the technical goals of high reliability, high accuracy, and miniaturization (Fig.4 Small Size (Ф18.2X23mm) Quartz Accelerometer For Aerospace), the following research areas are particularly crucial:
- Selection and testing of basic materials: Quartz (quartz glass, fused quartz), magnetic materials, piezoelectric ceramics, special alloys (low stress, high Q value), etc.
- Basic process research: Low-stress processing technology, low-stress packaging integration technology, material and component lifetime testing technology, etc.
- Basic algorithm research: Closed-loop control technology, calibration and compensation technology, calibration and testing technology, vibration rectification error suppression technology.
- Special high-temperature chip development: Low-noise reading chips for physical quantity conversion of sensitive units, analog-digital mixed control chips, etc.
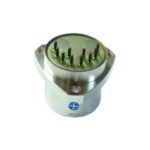
The quartz flexible accelerometer improves the material properties of existing sensitive structures, optimizes the temperature characteristics of quartz pendulums and magnetic steels, and determines the characteristics of new magnetic steels through research on the properties of high Curie temperature expansion alloy materials, high-temperature permanent magnet magnetic materials, high-temperature quartz pendulums, high-temperature adhesives, and high-temperature servo circuits. Starting from the top-level optimization design of the system, a new type of high-temperature mixed integrated circuit technology is developed, and calibration and calibration compensation methods at the system level and sensor level are established.
4. Conclusion:
Quartz accelerometers represent a critical advancement in the pursuit of precision and accuracy in petroleum logging. Their high sensitivity, reliability, and ability to mitigate environmental disturbances make them indispensable tools for acquiring precise data in the challenging environment of the borehole. Notably, ER-QA-03D mentioned above, a quartz accelerometer tailored for the oil and gas sector, manufactured by Ericco, finds widespread application in Measurement While Drilling (MWD) and oil well logging operations. As the oil and gas industry continues to push the boundaries of exploration and production, the integration of quartz accelerometers promises to further enhance subsurface characterization efforts, enabling operators to make more informed decisions and optimize production strategies with confidence.
Additionally, Ericco offers other products like ER-QA-03A, featuring bias repeatability of 10-50μg and scale factor repeatability of 15-50 ppm. ER-QA-03A is predominantly utilized in inertial measurement and testing systems across the aerospace and aviation industries. Beyond industrial applications, these accelerometers are instrumental in scientific research domains, facilitating the study of earthquakes, crustal movements, cosmology, and microgravity environments.
I will appreciate it if you find this article helps you a lot. Read the following articles to get more information bout quartz accelerometer.
Add Your Heading Text Here
1. How to Improve the Impact Resistance of Quartz Accelerometer
2. Temperature Error Analysis of Quartz Accelerometer
3. How to Improve the Long-term Stability of the Quartz Accelerometer?
4. Analysis of I/F Conversion Circuit of Quartz Accelerometer
5. What is the Effect of Temperature Coefficient on Quartz Accelerometer?
6. What are the Advantages and Disadvantages of Quartz Accelerometers?
Add Your Heading Text Here
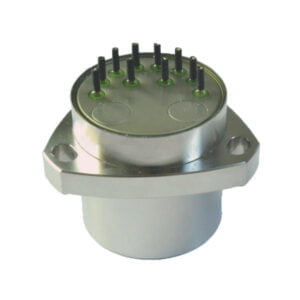
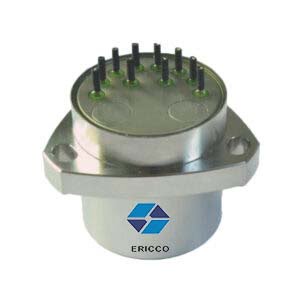
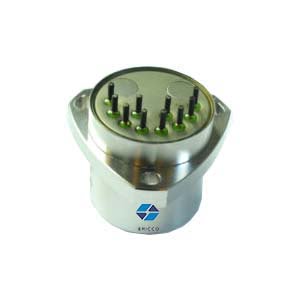
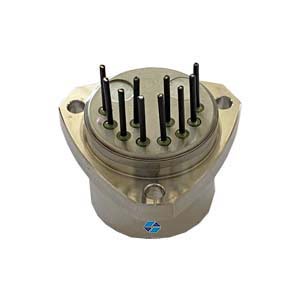
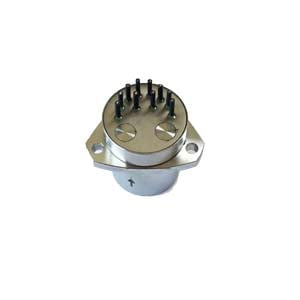
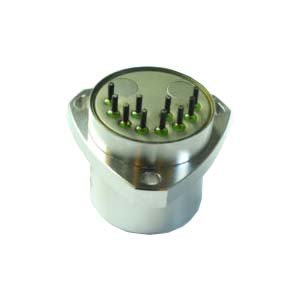