1.IMU measurement principle
IMU (Inertial Measurement Unit) is a device that can measure the angular velocity and acceleration of an object in three-dimensional space. Its core components usually include a three-axis gyroscope and a three-axis accelerometer. Gyroscopes are used to measure the angular velocity of an object about three orthogonal axes, while accelerometers are used to measure the acceleration of an object along three orthogonal axes. By integrating these measurements, the velocity, displacement and attitude information of the object can be obtained.
2.Pipe bending strain identification
In pipeline inspection, IMU can be used to identify the bending strain of the pipeline. When an IMU is installed on a pig or other mobile device and moves within a pipeline, it can sense changes in acceleration and angular velocity caused by pipeline bending. By analyzing this data, the degree and location of pipe bends can be identified.
3.Diameter measurement and pipe cleaning process
The diameter measuring and cleaning process is an important part of pipeline maintenance. In this process, a caliper pig equipped with an IMU is used to move along the pipeline, measure the inner diameter of the pipeline, and record the shape and size of the pipeline. This data can be used to assess the health of pipelines and predict possible maintenance needs.
4.Steel brush cleaning process
The steel brush pigging process is used to remove dirt and sediment from the inner walls of pipelines. In this process, a pig with a steel brush and an IMU moves along the pipeline, cleaning the inner wall of the pipeline through brushing and scouring. The IMU can record the geometric information and cleanliness of the pipeline during this process.
5.IMU detection process
The IMU inspection process is a key step in using IMU for data collection and measurement during pipeline maintenance. The IMU is installed on a pig or similar equipment and moves inside the pipeline while recording acceleration, angular velocity and other parameters. This data can be used to analyze the health of the pipeline, identify potential problems, and provide a basis for subsequent maintenance and management.
6.Data acquisition and post-processing
After completing the IMU detection process, the collected data need to be collected and post-processed. Data acquisition involves transferring raw data from the IMU device to a computer or other data processing device. Post-processing involves cleaning, calibrating, analyzing and visualizing the data. Through post-processing, useful information can be extracted from the original data, such as the shape, size, bending degree, etc. of the pipe.
7.Speed and attitude measurement
IMU can calculate the speed and attitude of an object by measuring acceleration and angular velocity. In pipeline inspection, measurement of speed and attitude is critical to assess the health of the pipeline and identify potential problems. By monitoring the speed and attitude changes of the pig in the pipeline, the shape, bending degree and possible obstacles of the pipeline can be inferred.
8.Pipe Curvature and Strain Assessment
Using the data measured by the IMU, the curvature and strain of the pipeline can be evaluated. By analyzing acceleration and angular velocity data, the radius of curvature and bending angle of the pipe at different locations can be calculated. At the same time, combined with the material properties and loading conditions of the pipe, the strain level and stress distribution of the pipe at the bend can also be evaluated. This information is important for predicting the life of pipelines, assessing safety, and developing maintenance plans.
Summarize
To sum up, IMU plays an important role in pipeline inspection. By measuring parameters such as acceleration and angular velocity, comprehensive assessment and maintenance of pipeline health can be achieved. With the continuous advancement of technology and the expansion of application fields, the application of IMU in pipeline inspection will become more and more extensive. The MEMS IMU independently developed by ERICCO has relatively high accuracy, such as ER-MIMU-01 and ER-MIMU-05, which are more accurate and are navigation-grade products. If you want to know more about IMU, please contact our professional technicians as soon as possible.
More Technical Questions
1.IMU working principle & Tactical grade IMU product recommendations
2.Choosing an IMU: FOG IMUs vs MEMS IMUs
3.Application of IMU in the Field of Drones
5.What is the Difference Between IMU and AHRS?
Products in Article
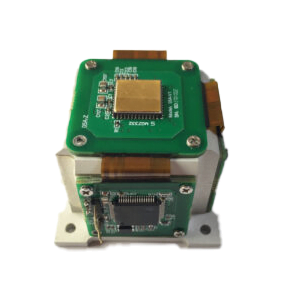
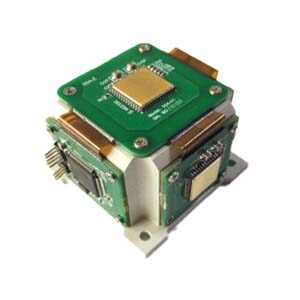
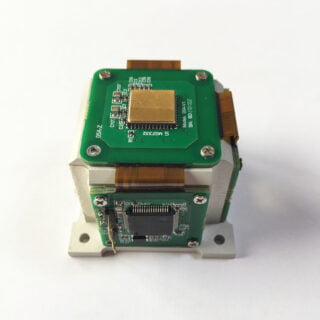
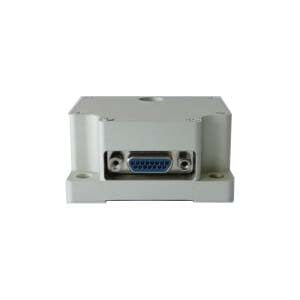
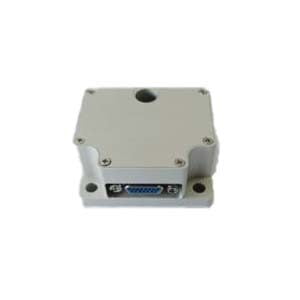
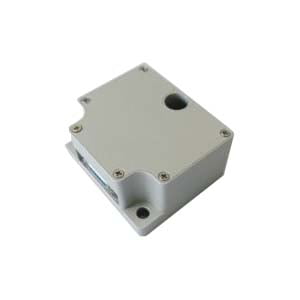