1.MEMS technology foundation
Microelectromechanical systems (MEMS) technology is a microsystem that integrates mechanical structures, sensors, actuators, and control circuits at the micron or nanoscale. It combines microelectronics technology and precision machining technology and is a key technology to achieve miniaturization, integration and intelligence. The foundation of MEMS technology includes micro-manufacturing technology, micro-structure design, micro-materials, etc. These technologies provide a solid foundation for the manufacturing of inertial measurement units.
2.Principle of inertial sensor
Inertial sensors are the core components of MEMS inertial measurement units, mainly including accelerometers and gyroscopes. The accelerometer indirectly obtains the object's motion state by measuring the acceleration it undergoes; the gyroscope reflects the object's rotation state by measuring the object's angular velocity. These sensors work based on Newton's second law and the principle of conservation of angular momentum, and are key to realizing navigation, positioning, attitude control and other functions.
3.System architecture design
The system architecture design of the inertial measurement unit needs to consider many aspects such as sensor selection, circuit design, and data processing. Sensor selection should select appropriate accelerometers and gyroscopes based on application requirements; circuit design should take into account factors such as low power consumption and high reliability; data processing involves signal collection, processing, and transmission. Reasonable architecture design is the key to ensuring stable and reliable performance of the inertial measurement unit.
4.Signal processing algorithm
Signal processing algorithm is the core of inertial measurement unit data processing. It involves signal filtering, fusion, calibration and other aspects. The filtering algorithm can effectively remove noise interference and improve measurement accuracy; the fusion algorithm can fuse data from different sensors to obtain more accurate and comprehensive motion status information; the calibration algorithm is used to correct sensor errors and improve measurement accuracy.
5.Error analysis and compensation
The error of the inertial sensor is a key factor affecting the measurement accuracy. Error sources mainly include temperature effects, nonlinear effects, scale factor errors, etc. Error analysis requires an in-depth understanding of the sources and impact of various errors to provide a basis for error compensation. Error compensation technology corrects errors through software or hardware means to improve the measurement accuracy of the inertial measurement unit.
6.System integration and packaging
System integration is the process of organically combining various functional modules to achieve overall functions. Packaging technology is to package the integrated system to protect the internal circuits and sensors and improve the reliability and stability of the product. System integration and packaging technology are of great significance for achieving miniaturization, integration, and high reliability of inertial measurement units.
7.Performance testing and evaluation
Performance testing and evaluation are important links in the development process of inertial measurement units. By testing the prototype, we can learn whether its performance indicators such as accuracy, stability, reliability, etc. meet the design requirements. The evaluation process requires the development of scientific evaluation standards and methods, and comprehensive analysis of test results to provide a basis for product optimization and improvement.
8.Application scenario expansion
Inertial measurement units have broad application prospects and can be used in aerospace, intelligent transportation, robot navigation, sports technology and other fields. With the advancement of technology and reduction of costs, its application scenarios will continue to expand. In future development, inertial measurement units are expected to play an important role in more fields and promote technological progress and industrial upgrading of related industries.
ERICCO's newly developed MEMS inertial measurement unit can be used in a variety of fields. For example, ER-MIMU-09 is mainly used as an IMU in the drilling field. ER-MIMU-01 navigation level IMU can be used in petroleum exploration and mining, etc.
If you want to know about the inertial measurement unit, please contact our relevant technical personnel.
More Technical Questions
1.IMU temperature drift removal algorithm
2.Adaptive method to detect vehicle motion status using MEMS-IMU
3.IMU denoising method based on wavelet and long short-term memory
4.IMU and GPS fusion algorithm principle
5.MEMS IMU error analysis and compensation
6.Reusable spacecraft IMU dynamic accuracy assessment method
Products in Article

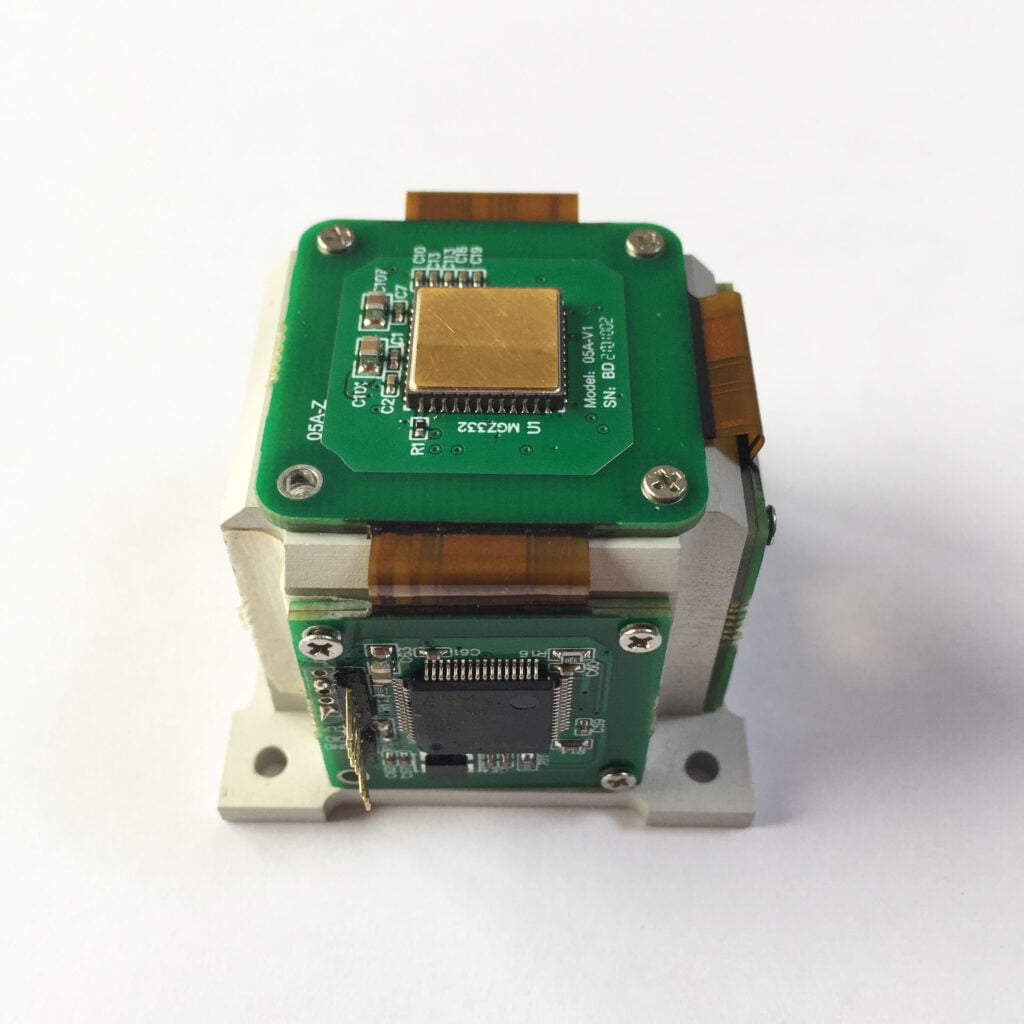
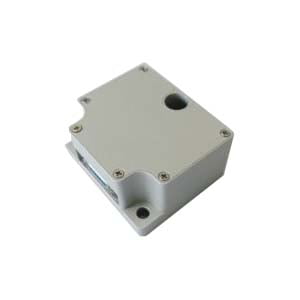
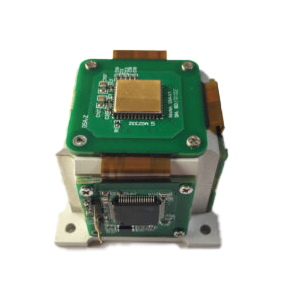
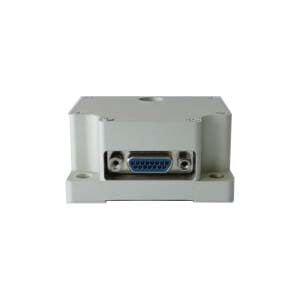
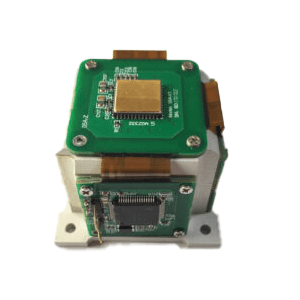