MEMS accelerometers have now advanced to the stage where they can effectively measure vibrations across a wide range of machinery platforms. Recent enhancements in their functionality, coupled with the numerous inherent advantages they possess over traditional vibration sensors (such as size, weight, cost-effectiveness, shock resistance, and user-friendliness), are driving the adoption of MEMS accelerometers in a burgeoning category of condition-based monitoring (CBM) systems.
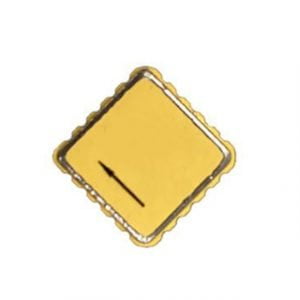
1.Understanding MEMS Accelerometers:
MEMS accelerometers are miniature sensors that detect changes in acceleration, enabling the measurement and analysis of mechanical vibrations. Unlike traditional piezoelectric accelerometers, which rely on bulky and expensive equipment, MEMS accelerometers boast a compact size, low cost, and remarkable sensitivity, making them ideal for a wide range of applications.
MEMS accelerometers typically consist of a microscopic mechanical structure suspended within a silicon chip. When subjected to acceleration, this structure experiences minute displacements, which are then converted into electrical signals proportional to the acceleration. This process allows MEMS accelerometers to capture even the smallest vibrations with exceptional accuracy.

2.Advantages Over Traditional Methods:
MEMS accelerometers offer several significant advantages, notably their compact size and exceptional sensitivity. These devices leverage microscopic components and advanced manufacturing techniques to achieve remarkably small dimensions, often measuring just a few millimeters across. This compactness is particularly advantageous in applications where space is limited, such as in UAVs and wearable devices.
Moreover, the small size of MEMS accelerometers enables seamless integration into various systems and structures, facilitating real-time monitoring without imposing burdensome weight or space requirements. This integration capability allows for continuous monitoring and analysis, empowering proactive maintenance practices and performance optimization across diverse industries.
In addition to their compact design, MEMS accelerometers exhibit high sensitivity, thanks to their utilization of miniature components. This heightened sensitivity enables precise measurement of even the smallest accelerations, making these sensors invaluable in applications demanding precise data, such as medical devices and aerospace technology. Notably, ER-MA-5, a high accuracy MEMS accelerometer, possesses bias stability of 5 μg.
The heightened sensitivity of MEMS accelerometers plays a crucial role in early detection of potential issues within mechanical systems, including imbalance, misalignment, or wear. By identifying these issues before they escalate, MEMS accelerometers help minimize downtime and extend the operational lifespan of equipment, ensuring optimal performance and reliability.
3.Diverse Applications:
The MEMS devices have a wide range of applications, since such systems have multiple sensing functions including temperature, pressure, acceleration and humidity sensing. In addition, these devices can be used to measure not only mechanical quantities but also electrical quantities by using capacitive MEMS. It was recognized already in 1990s that this enables important potential applications of these devices in electrical precision measurements and metrology.
Across industries such as automotive, aerospace, manufacturing, and structural health monitoring, these accelerometers play a pivotal role in ensuring the reliability and safety of mechanical systems.
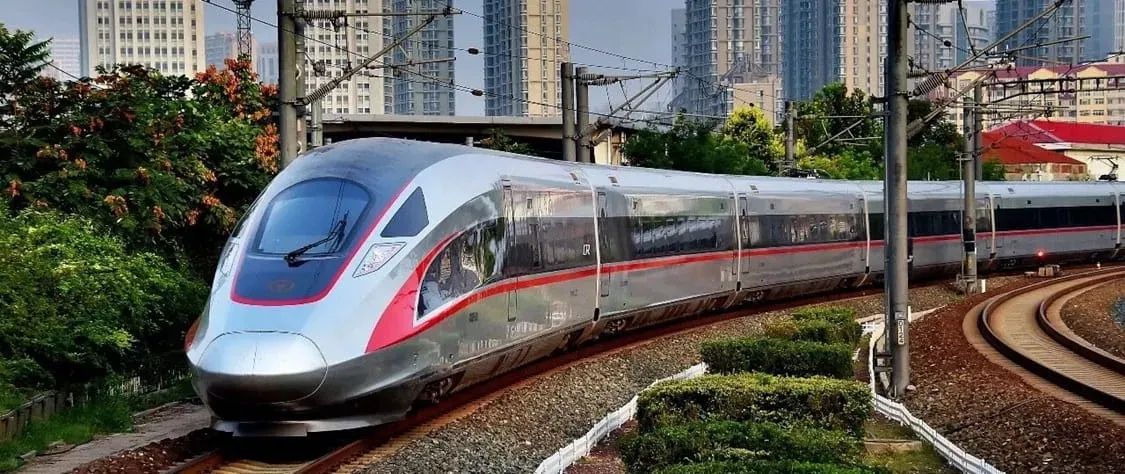
In the automotive sector, MEMS accelerometers are used for monitoring engine vibrations, analyzing vehicle dynamics, and detecting impacts in crash scenarios. In aerospace applications, these sensors enable precise attitude and position control, as well as structural health monitoring of aircraft components.
In manufacturing environments, MEMS accelerometers facilitate condition monitoring of machinery, detecting abnormalities in rotating equipment such as pumps, motors, and turbines. Moreover, in structural health monitoring, these sensors are deployed to assess the integrity of bridges, buildings, and other critical infrastructure, helping to identify potential structural defects and prevent catastrophic failures.
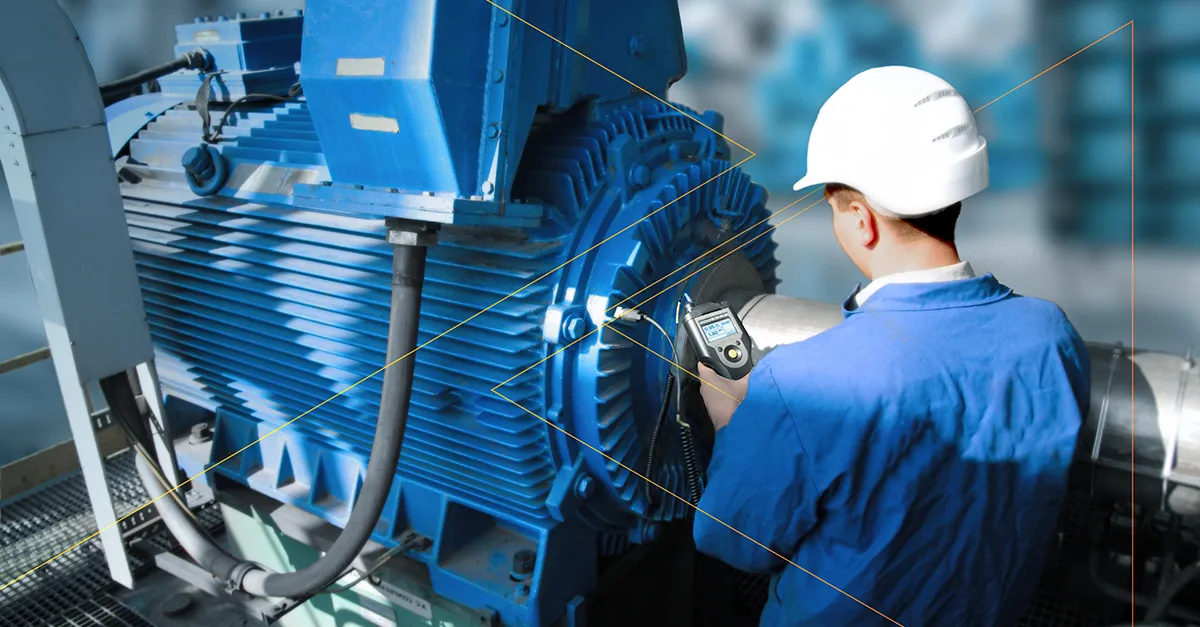
The ER-MA-5, as mentioned earlier, finds application across a spectrum of fields. It serves as a valuable tool for vibration measurement in various scenarios, including monitoring mechanical equipment, assessing structural integrity in bridges and dams, and conducting safety tests. Additionally, its utility extends to inertial guidance systems, where it aids in precise navigation and overload measurement. Moreover, the ER-MA-5 is employed in combined navigation systems for comprehensive positioning solutions.
Furthermore, its versatility shines in tilt measurement applications, such as determining antenna attitude, conducting platform measurements, and performing dip tests. This broad range of applications underscores the ER-MA-5's adaptability and reliability in diverse settings, making it a preferred choice for professionals across industries.
4.Challenges and Solutions:
Despite their numerous advantages, MEMS accelerometers also present challenges, particularly in applications where high accuracy is paramount. Factors such as temperature variations, sensor drift, and electromagnetic interference can impact the reliability of data collected.
To address these challenges, ongoing research and development efforts focus on improving sensor designs, enhancing signal processing algorithms, and implementing robust calibration techniques. Additionally, advancements in packaging and encapsulation technologies aim to enhance sensor durability and resilience to harsh operating environments.
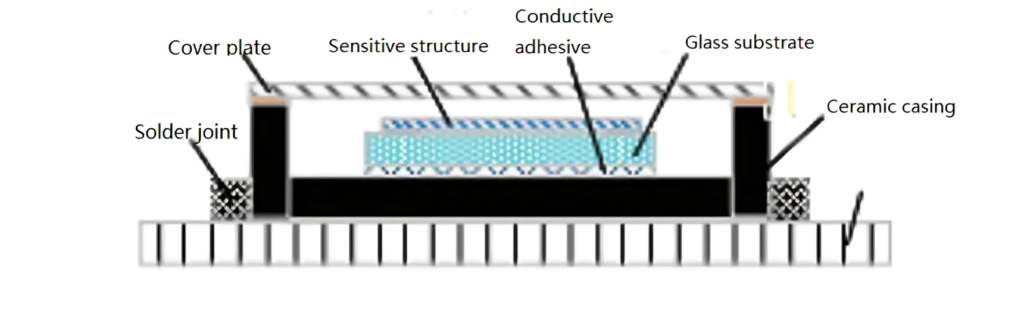
For example, the MEMS accelerometers have possible applications in navigation systems such as AHRS due to their characteristics already cited of small size, lightweight, low power and low cost. However, these sensors introduce great errors that must be compensated in order to make use of them in navigation systems.
Examples are shown in reference MEMS-based low-cost strap-down AHRS research where the results of an AHRS having low-cost MEMS based in a three-axis fight turntable table are shown and validated in a practical application where the system was mounted in a micro-Unmanned Aerial Vehicle (UAV), and the errors due to gyroscopic drift are detected and corrected by a multi-sensor data fusion algorithm that uses benchmark reference vectors.
5.Future Outlook:
As industries continue to prioritize efficiency, reliability, and safety, the demand for MEMS accelerometers is expected to rise. With ongoing advancements in sensor technology and data analytics, these tiny devices will play an increasingly integral role in monitoring and optimizing mechanical systems.
Future innovations in MEMS accelerometer technology may include enhanced multi-axis sensing capabilities, improved power efficiency, and integration with emerging technologies such as wireless communication and edge computing. These developments will further expand the applications of MEMS accelerometers, driving innovation and progress across diverse industries.
In conclusion, MEMS accelerometers have emerged as indispensable tools for analyzing mechanical vibrations, offering a potent combination of precision, versatility, and accessibility. As technology continues to evolve, these sensors will remain at the forefront of innovation, empowering engineers and researchers to unlock new insights and optimize the performance of mechanical systems.
I will appreciate it if you find this article helps you a lot. Read the following articles to get more information about accelerometer.
More Technical Questions
1. Analysis of Temperature Characteristics of Quartz Flexible Accelerometer
2. Failure Mode Analysis of Quartz Flexure Accelerometer
3. Improvement of Temperature Stability of Quartz Flexible Accelerometers
4. Quartz Accelerometers Advance Petroleum Logging Precision
5. Analysis of I/F Conversion Circuit of Quartz Accelerometer
6. MEMS Accelerometer Installation Error Correction Method
Products in Article
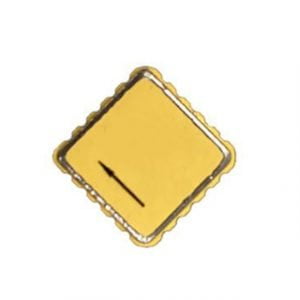

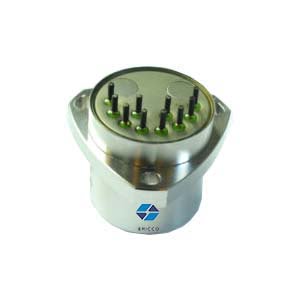
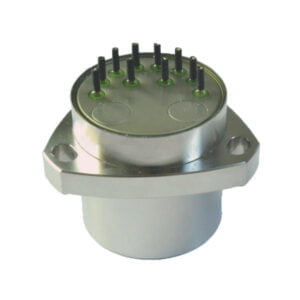
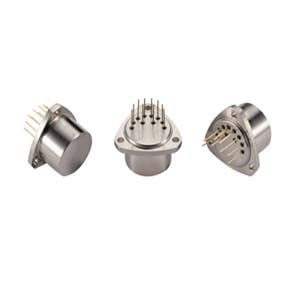
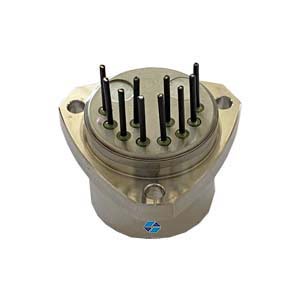