1.What is IMU?
An IMU, short for Inertial Measurement Unit, is a device that integrates multiple inertial sensors. It usually includes three main components: an accelerometer, a gyroscope, and a magnetometer. These sensors can measure an object's acceleration, angular velocity, and magnetic field strength in space, thereby providing information about the object's motion state and attitude.
Accelerometer: Used to measure the linear acceleration of the object in three axes, that is, the acceleration of the object changes in three directions.
Gyroscope: used to measure the angular speed of the object rotating around three axes, that is, the rotation of the object around three directions.
Magnetometer: Used to measure the effect of the Earth's magnetic field on an object, so as to determine the direction of the object's position relative to the Earth's magnetic field.
By integrating the data provided by these sensors, IMU can monitor and record the motion state of objects in real time, which is widely used in navigation systems, drones, robots, virtual reality and other fields.
2.IMU indicators
2.1 Accuracy
Accuracy is one of the important indexes to measure the performance of IMU. For accelerometers and gyroscopes, accuracy is usually expressed in terms of zero bias error and scale factor error.
Scale Factor error: The difference between the measured value and the true value of the sensor output. Zero bias error results in a fixed deviation from the measured result.
Scale factor error: The proportional relationship between the measured value output by the sensor and the true value is not accurate. Scale factor error will cause the measurement result to produce scaling deviation.
The accuracy of magnetometer is mainly measured by scale factor error and non-orthogonality error.
Scale factor error: The proportional relationship between the sensor output value and the true magnetic field strength is not accurate.
Non-orthogonality error: there is a non-ideal orthogonality between the three axes of the magnetometer.
2.2 Dynamic Range
The dynamic range is the range between the maximum and minimum physical quantities that the IMU can measure. For accelerometers, dynamic range is usually expressed in g and represents the maximum acceleration that can be measured relative to the acceleration of gravity (about 9.8 m/s²). For gyroscopes, dynamic range is usually measured in angular velocity, representing the maximum angular velocity that can be measured.
The large dynamic range means that the IMU can measure changes in physical quantities over a wider range, improving its applicability and the breadth of application scenarios.
2.3 Frequency Response
Frequency response is the ability of the IMU to respond to changes in the frequency of the input signal. For accelerometers and gyroscopes, the frequency response is usually expressed in terms of bandwidth, that is, the maximum frequency that can be accurately measured. The higher the bandwidth, the higher the measurement accuracy of the IMU at high frequency signals.
2.4 Sampling Rate
Sampling rate refers to the frequency at which the IMU samples the sensor data. Higher sampling rates can provide finer data analysis and processing capabilities, but also increase data processing and storage requirements.
2.5 Temperature Stability
Temperature stability refers to the stability of the output value of the IMU under different temperature environments. Temperature changes may cause drift or deviation of sensor output values, affecting the accuracy of IMU measurement results. Better temperature stability can provide more reliable measurement results.
3.IMU application
3.1 Navigation System
Imus play an important role in navigation systems and can estimate an object's position, speed and attitude by measuring its acceleration and angular velocity. Combined with other sensors (such as GPS), IMU can provide more accurate navigation information, which is widely used in automotive navigation, aircraft navigation, unmanned vehicles and other fields.
3.2 UAV
The UAV needs to monitor its own motion status and attitude in real time to maintain a stable flight. As one of the key components, IMU can provide high-precision attitude information to help UAV achieve autonomous control, obstacle avoidance and other functions.
3.3 Robot
IMU is also widely used in the field of robotics. By acquiring the acceleration and angular velocity information of the object, the robot can sense the surrounding environment and make corresponding actions. For example, in industrial production, IMU can be used to detect the position and attitude of a robot arm for accurate operation.
3.4 Virtual Reality
Virtual reality technology needs to track the movement of the user's head in real time to present a realistic virtual world. As one of the common sensors in head-mounted devices, IMU can provide high frequency and low latency attitude information to enhance the user experience.
Summary
As a device integrating multiple inertial sensors, IMU can measure the acceleration, angular velocity and magnetic field strength of an object, providing information about the motion state and attitude of the object. IMU specifications include accuracy, dynamic range, frequency response, sampling rate and temperature stability. It has a wide range of applications in navigation systems, drones, robots and other fields. The MEMS IMU independently developed by ERICCO can be applied to the positioning and orientation of drones and navigation fields, such as ER-MIMU-01 as a navigation-level IMU with high accuracy, which can be used in Bridges, high-rise buildings, towers, dam monitoring, geotechnical monitoring, mining and so on.
If you want to talk about or purchase MEMS IMU, please contact our relevant technical personnel.
More Technical Questions
1.IMU working principle & Tactical grade IMU product recommendations
2.Choosing an IMU: FOG IMUs vs MEMS IMUs
3.Application of IMU in the Field of Drones
5.What is the Difference Between IMU and AHRS?
Products in Article
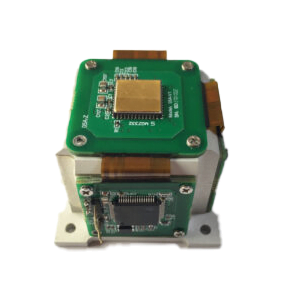
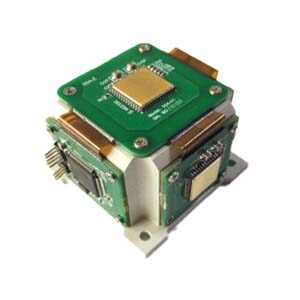
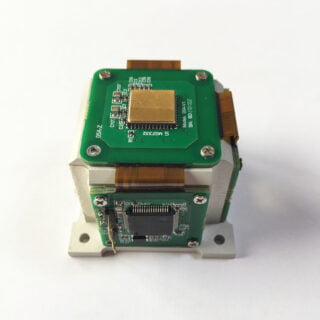
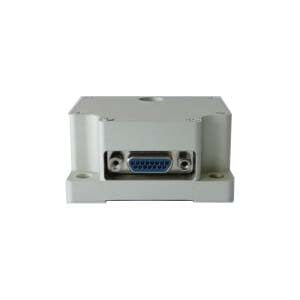
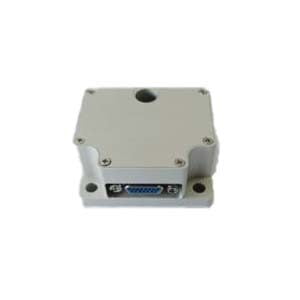
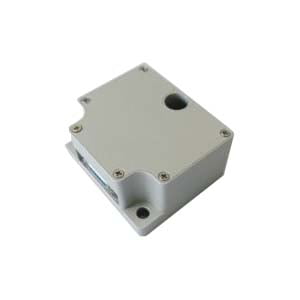