Tilt sensor is an important tool for measuring inclination Angle, which is widely used in industry and military, such as the Angle measurement of missile launching guide rail, the attitude measurement of ship navigation, etc.
In reality, the measurement of the Angle of the inclinometer sensor is focused on the accuracy of the measurement, so it becomes particularly important to improve the measurement accuracy. The working environment temperature of the tilt sensor changes greatly, and the measurement error caused by the working temperature accounts for a large proportion of the overall error, so this paper mainly analyzes and tests the temperature characteristics of the sensor.
It is found that the accelerometer, the analog-to-digital converter and the whole sensor housing have a serious influence on the measurement accuracy of the sensor. On this basis, we propose a method combining least square method and piecewise linearization for temperature compensation, which greatly improves the measurement accuracy.
1. Temperature characteristics of the sensor
The overall measurement process of the inclinometer sensor is the required data measured by the main measurement unit accelerometer, sent to the analog-to-digital (A/D) converter for processing, and then sent to the MCU together with the temperature sensor data for processing, and finally displayed by the communication unit. Accelerometer is the main tool to calculate the Angle and the basis of the realization of the tilt sensor. Second A/D converter
Related to the overall resolution and accuracy, they are greatly affected by temperature, is the main consideration.
1.1 Analysis from the overall perspective
When the tilt sensor is actually measured, it is to put the whole on a platform for Angle measurement, so the consistency of the inclinometer sensor base and the placement platform has a great impact on the overall measurement. For cost considerations, the base of the inclinometer sensor is generally made of aluminum alloy, and this material will expand and shrink with the change of external temperature, which directly affects the measurement of Angle.
1.2 Analysis from the main measurement unit
Accelerometer is the main measuring tool of sensor. It has the advantages of high precision, small size and wide operating temperature range. Because the working environment of its application is generally harsh, the temperature has become the main factor restricting the measurement accuracy. The influence of temperature on the accelerometer is that the change of temperature will affect the deformation of the accelerometer and the change of physical parameters, such as the torque length, magnetic induction intensity, resistivity, etc.
1.3 Analysis from the perspective of data processing
The A/D converter we choose is model CS5532, which converts the analog voltage value collected by the accelerometer into a digital signal for data processing by the MCU, and meets the basic technical requirements of the tilt sensor design. Assuming the accuracy of the A/D converter is n, the output voltage of the accelerometer is Vout, and the reference voltage of A/D is Vref, then there is an output value:
As can be seen from equation (6), if the reference voltage changes, it will inevitably affect the subsequent Angle calculation
REF195 Temperature related technical manual
(Vs=3.3V, -40℃≤ TA ≤ +85℃)
According to customer requirements for product accuracy, speed, etc., the inclinometer sensor selects REF195 E series chips to provide reference voltage Vref for A/D. Consult the relevant technical manual of REF195 (Table 1), and find that REF195 is affected by temperature, thus affecting Vref. In this paper, the sensor is selected to work at -40°~60°, and the formula for calculating the influence of temperature on REF195 is as follows:
When the typical value of temperature influence is 2
ΔU=1×10-3 V=1mV, In other words, the reference voltage varies from 1 to 2.5mV, which shows that the reference voltage has a certain influence on the output value of the ADC.
2. Temperature test of tilt sensor
According to the working conditions of the device, the temperature test range is -40 ° C ~60 ° C, and the Angle measurement range is from -10° to 110° every 20°. The temperature test is mainly carried out through the high and low temperature chamber. The first test: due to the temperature difference between the inside and outside of the sensor, in order to ensure the accuracy and accuracy of the measurement, after each adjustment of the temperature of the temperature box, wait 2h to make the internal temperature of the inclinometer sensor and the temperature of the temperature box consistent before measuring the Angle. Put a sensor in
After the initial calibration, the measurement data are shown in Table 2.
As can be seen from Table 2, even after the initial calibration of the inclinometer sensor, its actual Angle measurement value still has a large deviation from the real value (that is, the given value). Near a lower or higher temperature, the greater the deviation, it is necessary to prove the research on the temperature characteristics of the inclination sensor. The following paper presents a compensation algorithm for the influence of temperature on Angle measurement.
All parts except sinθ are treated as a whole Xt0, and the general expression between the sensor measurement Angle and the ADC output is obtained by synthesizing other temperature factors that cannot be summarized in Xt0:
AD=Xt0sin(θ0+θt)+Xt (7)
3. Error compensation ideas
We use the least square method and piecewise linearization to compensate the error caused by temperature. The compensation idea is:
(1) First, the A/D value of the temperature box at the given Angle θ0 is 0°, 60° and 90°, and according to the relationship between the above two, the initial calibration of Xt0, θt and Xt is preliminarily calculated, so that the Angle measured by the sensor will not deviate too much;
(2) On the base of the preceding one, use the temperature box to collect the temperature between -40 ° C and 60 ° C at an interval of 10° C each time, and measure the Angle value measured by the initially calibrated tilt sensor when the given Angle range is -10°~110° at an interval of 5° each time. A total of 11×25=275 data were analyzed and compensated;
(3) According to different given angles and measurement angles at each temperature, the least square method is used to find out the relationship between the two. In practice, the sensor can only obtain the measured value, then it is necessary to find out when the Angle measurement value is -10°~110°, calculate the given value of the sensor, the difference between the measured value and the given value is the error compensation value, and the measurement Angle is compensated.
(4) Through the above process, when the temperature range is -40 ° C ~60 ° C and the expected measurement Angle of the sensor is -10° C ~110°, the error compensation value corresponding to different temperatures and different angles is an array of 25×11. In actual measurement, according to the measured value of the sensor and the temperature value at that time, the piecewise linearization is used to find out the corresponding value of the array is the current compensation value, and the Angle compensation is carried out. According to the above steps, the error compensation value of the sensor obtained in this paper is shown in Figure 4, which represents the error compensation value when the temperature range is -40 ° C to 60 ° C every 10° C, and the measurement Angle range is -10° C to 110° every 5°. The measurement Angle is compensated by the error compensation value, and the error between the final measurement Angle and the real Angle is obtained, as shown in Figure 5. As can be seen from Figure 5, the temperature error compensation method we mentioned can well reduce the measurement error and control the error range within ±0.006° to meet the actual requirements of customers.
4 Summarize
The temperature characteristics of the tilt sensor are analyzed, and the effect of temperature on the measurement Angle is shown by experiments. Ericco's popular products ER-TS-3160VO and ER-TS-4158CU can all use the temperature error compensation method that integrates the least square method and piecewise linearization proposed above, because the above experiments have proved that this method can effectively control the measurement error between ±0.006°. The measurement error is well reduced, so that the measurement accuracy of the inclinometer sensor can be improved.
More Technical Questions
1.Stability Test and Analysis of Tilt Sensor
2.How to Improve Reliability of Tilt Sensors
3.Tilt Sensor Automatic Calibration System
4.Research on Angle Control Technology of Tilt Sensor
5.Tilt sensor, Tilt Switch&Other Common Problems in Installation and Use Process
6.Application of Tilt Sensor in Vehicle Four-wheel Positioning
Products in Article

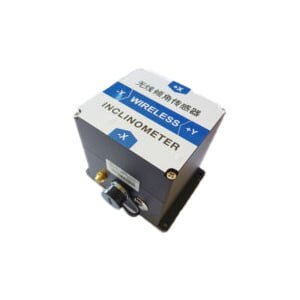
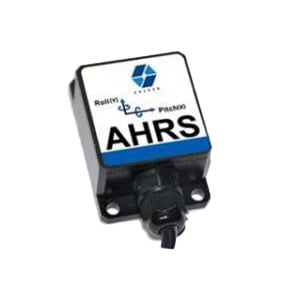
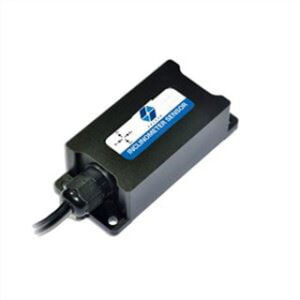

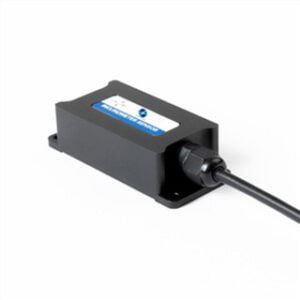