The precision of Q-Flex accelerometer is closely related to the processing and assembly accuracy during production. Accelerometers are instruments with complex production processes, and a significant number of uncertain factors are introduced during processing and assembly. A specific analysis of these factors helps improve the accuracy of accelerometers.
1.Processing Techniques
Compared to other precision instruments, the components of Q-Flex accelerometers have thin walls, high precision, complex shape features, and small dimensions. During the processing and assembly process, their manufacturing accuracy, shape errors, and dimensional precision are all at the micron level. They also involve the conversion of multiple physical parameters during operation and exhibit the characteristics of coupling effects between multiple physical fields.
During these conversions and coupling effects, components with corresponding physical properties are undoubtedly required. However, these components introduce some uncertain factors during assembly, inevitably leading to minor errors in the entire process. Since accelerometers themselves have a compact structure, these minor errors will inevitably affect the performance of the accelerometer.
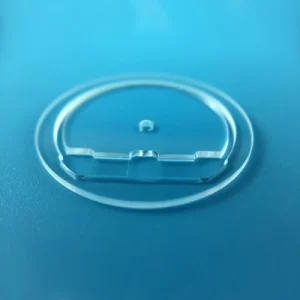
Quartz wafers and permanent magnets are core precision components of Q-Flex accelerometers, and their processing accuracy and performance directly affect the performance of the entire system. Quartz crystal is the main component of quartz wafers, which is a brittle non-metallic material with characteristics of high strength, high hardness, low conductivity, and low fracture toughness. Unlike common metal materials, the processing method greatly affects its strength, and any improper processing technique will affect the reliability, fracture strength, and surface integrity of quartz.
Currently, the commonly used processing methods are laser cutting combined with chemical etching. This method utilizes chemical etching technology to corrode beams and C-shaped grooves without residual stress. Laser trimming is then used for smooth cutting with high speed. However, this method involves multiple procedures such as sealing, masking, and clamping, making it a complex process. Experienced workers are required to accurately control the etching time and acid temperature, and it is prone to produce defective products.
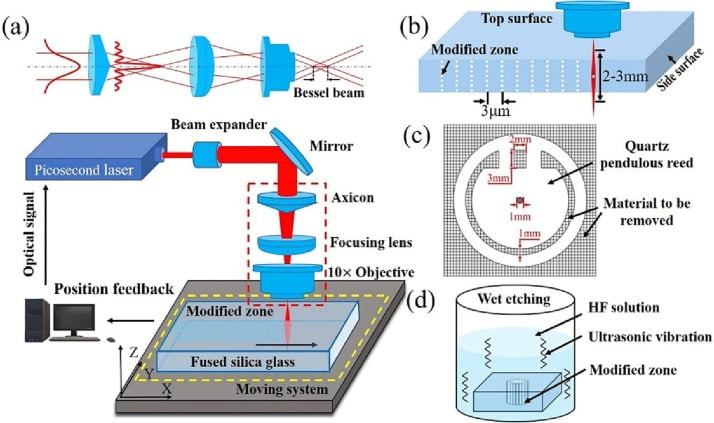
Compared to the very thin quartz beams, this method tends to result in higher surface roughness and uneven bending stress. Therefore, researching new processing techniques is necessary to improve processing accuracy and efficiency.
2.Assembly Process Techniques
Q-Flex accelerometers are highly precise instruments, and the quality of their assembly process directly determines the performance of the accelerometer. Currently, traditional manual assembly methods are still used for accelerometer assembly, with little innovation in assembly process techniques despite minor adjustments over the years. Designers and process engineers lack a systematic understanding of the impact of assembly process techniques on performance, leading to a lack of scientificity in establishing assembly processes.
The current assembly process for producing accelerometers follows a process of assembly first, then testing. However, due to the complexity of the assembly process, it is difficult to accurately identify factors leading to performance degradation. Moreover, the performance is closely related to the operation habits, skills, experience, and proficiency of assembly workers, resulting in the performance of produced accelerometers being approximately normally distributed, with a low rate of superior products. Even the use of high-precision components does not necessarily guarantee the assembly of accelerometers with superior performance.
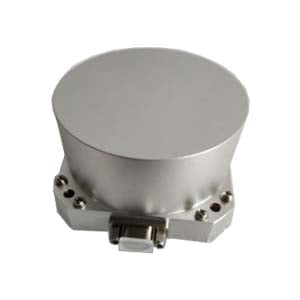
Furthermore, to design Q-Flex accelerometers with high precision over a small range, and to improve the overall performance of accelerometers, it is necessary to consider the extent to which processing and assembly techniques affect their performance. Scientifically improving the processing techniques and assembly processes of accelerometers is essential to reduce manufacturing complexity.
3.Summary
The precision of quartz flexure accelerometers relies on meticulous processing and assembly techniques. Accelerometers undergo complex manufacturing processes, where uncertainties affect precision. Systematic improvements in precision machining of core components are crucial. Additionally, the assembly process significantly impacts performance, requiring scientific advancements to reduce manufacturing complexity and enhance overall performance consistency.
It's worth noting that the zero bias repeatability of the quartz flexure accelerometer ER-QA-01A is 10μg, and the scale factor repeatability is 10ppm. It is applied in aircraft carrier microgravity measurement systems, inertial navigation systems, and static angle measurement systems.
More Technical Questions
1. Optimizing Compensation Loop for Quartz Accelerometer
2. 2 Ways to Improve Shock Resistance Performance of Q-Flex Accelerometer
3. Parameters to Evaluate Performance of Quartz Flexure Accelerometers
4. Factors Affecting the Stability of Q-Flex Accelerometers
5. Structure Design of High Precision Quartz Flexible Accelerometer
6. Methods to Maintain the Long-Term Performance of Quartz Flexure Accelerometers
Products In Article

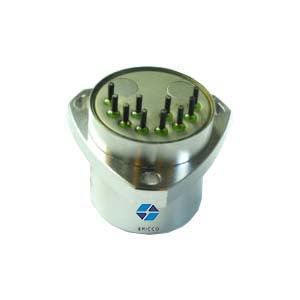
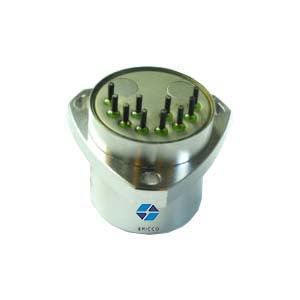
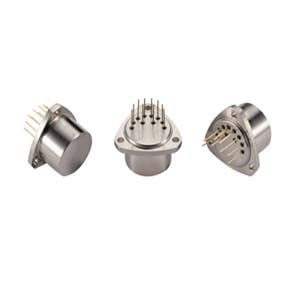
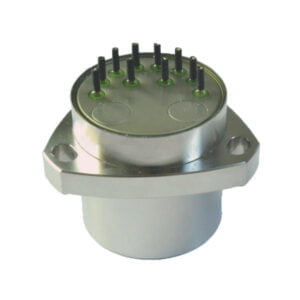
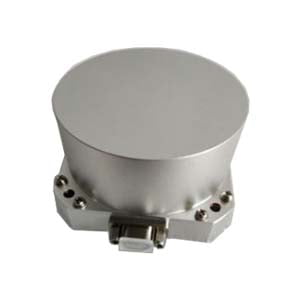